Method for preparing barium tungsten electrode
An electrode, barium tungsten technology, which is applied in the field of barium tungsten electrode preparation, can solve the problems of high production cost and complicated preparation process of tungsten sponge, and achieve the effects of prolonging service life, easy control of product quality, and enhanced light intensity
- Summary
- Abstract
- Description
- Claims
- Application Information
AI Technical Summary
Problems solved by technology
Method used
Examples
preparation example Construction
[0020] A preparation method of a barium tungsten electrode, comprising the following steps:
[0021] 1) using a volatile solvent to dissolve the paraffin to obtain a paraffin solution;
[0022] 2) Ba(Ca)ZrO 3 powder, tungsten powder, and paraffin solution are evenly mixed, the solvent is removed, the mixed powder obtained is poured into an electrode mold, and pressed;
[0023] 3) Heat the pressed electrode to 500-600°C at a rate of 100-150°C / hour, then heat it to 1300-1500°C at a rate of 190-200°C / hour and keep it warm for 0.6-1.3 hours, then heat it to 1800 ~2000℃ for 15~30 minutes;
[0024] 4) Treat the electrode with hydrogen at 1250-1350°C for 10-20 minutes to obtain a barium-tungsten electrode.
[0025] Preferably, Ba(Ca)ZrO 3 Powder: tungsten powder: paraffin wax=5~7:88~96:2~4 (mass ratio).
[0026] If the surface of the electrode becomes dark and black after the hydrogen burning treatment, put the electrode back in a vacuum resistance furnace and heat it to 1800-20...
Embodiment 1
[0037] 1) Dissolve 3 parts of paraffin with gasoline to obtain a paraffin solution;
[0038] 2) Add 5 parts of Ba(Ca)ZrO to the paraffin solution 3 Powder, 92 parts of tungsten powder, mix evenly, heat to make gasoline completely volatilize, wherein, tungsten powder is doped with 0.30% Al 2 o 3 pink;
[0039] 3) Pour the obtained mixed powder into the electrode mold at 15T / cm 2 The pressure is pressed to obtain the electrode;
[0040] 4) Heat the pressed electrode to 600°C at a rate of 120-130°C / hour in a vacuum resistance furnace, then heat it to 1400°C at a rate of 190-200°C / hour and keep it for 1 hour, then heat it to 1900°C keep warm for 20 minutes;
[0041] 5) Treat the electrode with hydrogen at 1250-1350°C for 10-20 minutes to obtain a barium-tungsten electrode.
Embodiment 2
[0043] 1) Dissolve 2 parts of paraffin with gasoline to obtain a paraffin solution;
[0044] 2) Add 7 parts of Ba(Ca)ZrO to the paraffin solution 3 Powder, 88 parts of tungsten powder, mix evenly, heat to make gasoline completely volatilize, wherein, tungsten powder is doped with 0.25% Al 2 o 3 pink;
[0045] 3) Pour the obtained mixed powder into the electrode mold at 12T / cm 2 The pressure is pressed to obtain the electrode;
[0046] 4) Heat the pressed electrode to 550°C at a rate of 140-150°C / hour in a vacuum resistance furnace, then heat it to 1500°C at a rate of 190-200°C / hour and keep it for 0.6 hours, then heat it to 2000°C keep warm for 15 minutes;
[0047] 5) Treat the electrode with hydrogen at 1250-1350°C for 10-20 minutes to obtain a barium-tungsten electrode.
PUM
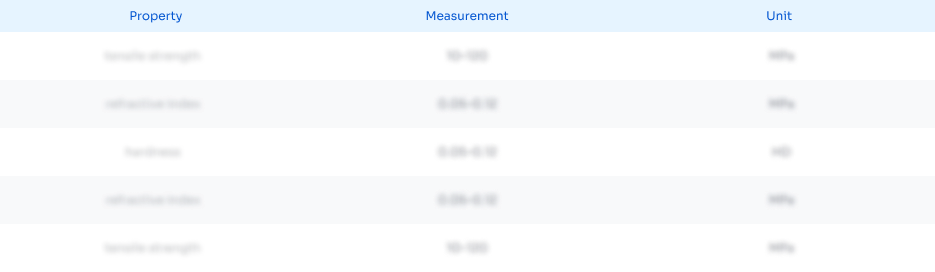
Abstract
Description
Claims
Application Information

- R&D
- Intellectual Property
- Life Sciences
- Materials
- Tech Scout
- Unparalleled Data Quality
- Higher Quality Content
- 60% Fewer Hallucinations
Browse by: Latest US Patents, China's latest patents, Technical Efficacy Thesaurus, Application Domain, Technology Topic, Popular Technical Reports.
© 2025 PatSnap. All rights reserved.Legal|Privacy policy|Modern Slavery Act Transparency Statement|Sitemap|About US| Contact US: help@patsnap.com