Milling force modeling method for titanium alloy TC18 milling process
A TC18, modeling method technology, applied in special data processing applications, instruments, electrical digital data processing, etc., can solve the problem that the non-zero milling force with equal phase width of the tool cannot be effectively simulated
- Summary
- Abstract
- Description
- Claims
- Application Information
AI Technical Summary
Problems solved by technology
Method used
Image
Examples
Embodiment 1
[0077] (1) Select the parameters of the end mill: the tool radius R is 6mm, the helix angle β is 37 degrees, the bottom edge inclination angle η is 3 degrees, and the number of tool teeth is N f is 4; milling method: down milling. Set the cutting parameters: the tool spindle speed is 600RPM, the single tooth feed rate is 0.0625mm / tooth, the axial cutting depth Rz is equal to 0.4mm, and the radial cutting depth Rr is equal to 2mm.
[0078] (2) Divide the milling cutter into 400 equal-height beam segments in the axial direction, and calculate the tangential milling force F acting on the j-th side edge unit on the i-th tooth at time t by the following formula T,F,i,j (t) and radial milling force F R,F,i,j (t):
[0079] f T,F,i,j (t)=K T,F,i,j h F,i,j (t)w z
[0080] f R,F,i,j (t)=K R,F,j,j h F,i,j (t)w z
[0081] In the formula, K T,F,i,j is the tangential milling force coefficient corresponding to the jth side edge unit on the ith tooth, K R,F,i,j is the radial mil...
Embodiment 2
[0130] (1) Select the parameters of the end mill: the tool radius R is 6mm, the helix angle β is 37 degrees, the bottom edge inclination angle η is 3 degrees, and the number of tool teeth is N f is 4; milling method: down milling. Set the cutting parameters: the tool spindle speed is 800RPM, the single tooth feed rate is 0.03125mm / tooth, the axial cutting depth Rz is equal to 0.4mm, and the radial cutting depth Rr is equal to 2.5mm.
[0131] (2) Divide the milling cutter into 400 equal-height beam segments in the axial direction, and calculate the tangential milling force F acting on the j-th side edge unit on the i-th tooth at time t by the following formula T,F,i,j (t) and radial milling force F R,F,i,j (t):
[0132] f T,F,i,j (t)=K T,F,i,j h F,i,j (t)w z
[0133] f R,F,i,j (t)=K R,F,i,j h F,i,j (t)w z
[0134] In the formula, K T,F,i,j is the tangential milling force coefficient corresponding to the jth side edge unit on the ith tooth, K R,F,i,j is the radial ...
PUM
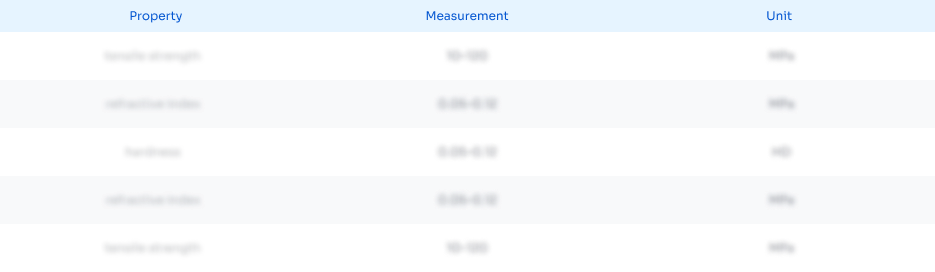
Abstract
Description
Claims
Application Information

- Generate Ideas
- Intellectual Property
- Life Sciences
- Materials
- Tech Scout
- Unparalleled Data Quality
- Higher Quality Content
- 60% Fewer Hallucinations
Browse by: Latest US Patents, China's latest patents, Technical Efficacy Thesaurus, Application Domain, Technology Topic, Popular Technical Reports.
© 2025 PatSnap. All rights reserved.Legal|Privacy policy|Modern Slavery Act Transparency Statement|Sitemap|About US| Contact US: help@patsnap.com