Smelting method for low-silicon ultralow-sulphur steel
A technology of ultra-low sulfur steel and smelting method, which is applied in the field of metallurgy, can solve problems such as easy silicon increase, and achieve the effect of reducing the amount of silicon increase
- Summary
- Abstract
- Description
- Claims
- Application Information
AI Technical Summary
Problems solved by technology
Method used
Examples
Embodiment 1
[0032] 1) After pretreatment of KR molten iron, the sulfur content is 0.002%, and the slag removal rate is >95%;
[0033] 2) The silicon content of molten iron after dephosphorization converter smelting is 0.003%;
[0034] 3) The sulfur content of molten steel at the end of decarburization converter smelting is 0.011%, and the basicity of slag is 4.6;
[0035] 4) When the tapping amount is 1 / 5, add 810Kg of small lime lime and 202Kg of fluorite;
[0036] 5) Add 1.2 tons of aluminum and iron when the tapping amount is 2 / 5;
[0037] 6) Sampling and analysis of sulfur content after tapping is 0.0096%, and acid-soluble aluminum content is 0.046%;
[0038] 7) LF refining has not carried out aluminum adjustment operation, the slag alkalinity of the incoming slag is 6.2, and the total iron content is 1.02%;
[0039] 8) Add 2000Kg of small lime, 500Kg of fluorite, 8.6 alkalinity of refining slag, and 0.3% total iron content in the LF refining process;
[0040] 9) After the LF refi...
Embodiment 2
[0042] 1) After KR molten iron pretreatment, the sulfur content is 0.001%, and the slag removal rate is >95%;
[0043] 2) The silicon content of molten iron after dephosphorization converter smelting is 0.002%;
[0044] 3) The sulfur content of molten steel at the end of decarburization converter smelting is 0.011%, and the basicity of slag is 4.4;
[0045] 4) Add 789Kg of small-grain lime and 205Kg of fluorite when the tapping amount is 1 / 5;
[0046] 5) Add 1.3 tons of aluminum and iron when the tapping amount is 2 / 5;
[0047] 6) Sampling and analysis of sulfur content after tapping is 0.0078%, and acid-soluble aluminum content is 0.048%;
[0048]7) LF refining has not carried out aluminum adjustment operation, the slag alkalinity of the incoming slag is 6.5, and the total iron content is 0.94%;
[0049] 8) Add 1500Kg of small lime, 250Kg of fluorite, 6.9 alkalinity of refining slag, and 0.2% total iron content in the LF refining process;
[0050] 9) After the LF refining...
PUM
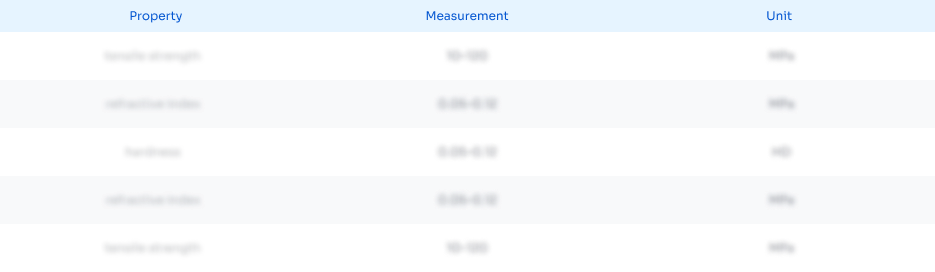
Abstract
Description
Claims
Application Information

- R&D
- Intellectual Property
- Life Sciences
- Materials
- Tech Scout
- Unparalleled Data Quality
- Higher Quality Content
- 60% Fewer Hallucinations
Browse by: Latest US Patents, China's latest patents, Technical Efficacy Thesaurus, Application Domain, Technology Topic, Popular Technical Reports.
© 2025 PatSnap. All rights reserved.Legal|Privacy policy|Modern Slavery Act Transparency Statement|Sitemap|About US| Contact US: help@patsnap.com