Method for forming integral panel of main body
A technology of integral siding and forming method, applied in the field of forming integral siding of the fuselage, can solve the problems of parts and tools prone to resonance, parts failure, etc., and achieve the effect of reliable quality, low value, and improved product quality
- Summary
- Abstract
- Description
- Claims
- Application Information
AI Technical Summary
Problems solved by technology
Method used
Image
Examples
Embodiment Construction
[0013] refer to figure 1 . The outer surface of the integral wall plate part on the right side of the fuselage is an aircraft single-curvature aerodynamic shape, and only the inner surface is processed. More than 400 coordination holes need to be drilled on the siding for positioning frames, stringers and other parts, and the cutouts around the siding and door frames and window frames are of precise shape. According to the present invention, the curvature of the integral wall panel of the fuselage is first formed by rolling forming equipment; before rolling, it is confirmed whether the raw material for manufacturing the integral wall panel is flat and whether the thickness dimension meets the requirements. If it does not meet the flatness and thickness requirements, then proceed Supplementary milling processing to pass and then rolling forming. If the raw material meets the requirements, roll bending is performed directly. The integral wall panel is processed in a flat unfo...
PUM
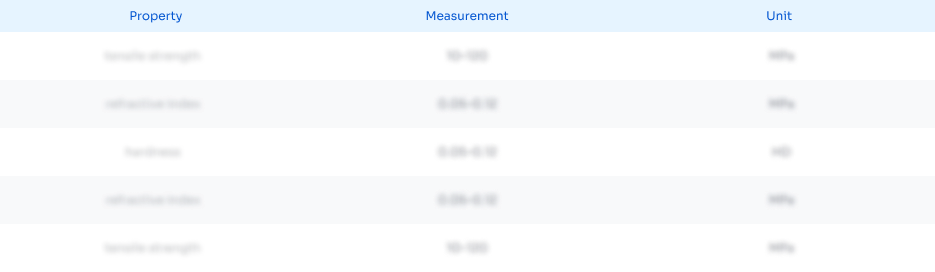
Abstract
Description
Claims
Application Information

- R&D
- Intellectual Property
- Life Sciences
- Materials
- Tech Scout
- Unparalleled Data Quality
- Higher Quality Content
- 60% Fewer Hallucinations
Browse by: Latest US Patents, China's latest patents, Technical Efficacy Thesaurus, Application Domain, Technology Topic, Popular Technical Reports.
© 2025 PatSnap. All rights reserved.Legal|Privacy policy|Modern Slavery Act Transparency Statement|Sitemap|About US| Contact US: help@patsnap.com