Asymptotic variational method-based method for simulating and optimizing composite material laminated plate
A composite material layer, asymptotic variational method technology, applied in the field of optimization design, can solve the problems of unpredictable stress distribution, low analysis efficiency, small amount of calculation, etc., to improve the speed and efficiency of the solution, high versatility, The effect of increasing the buckling critical load
- Summary
- Abstract
- Description
- Claims
- Application Information
AI Technical Summary
Problems solved by technology
Method used
Image
Examples
Embodiment Construction
[0023] The present invention will be further described below in conjunction with specific examples and accompanying drawings.
[0024] 1. Three-dimensional expression
[0025] see figure 2 , is the coordinate system diagram before and after plate deformation. The position of any point on the reference plane of the composite laminate can be determined by its Cartesian coordinate system x i means, among them, x α are mutually orthogonal coordinates on the datum plane, x 3 It is the normal coordinate (letter subscripts i, j, k represent 1, 2, 3; letter subscripts α, β represent 1, 2, the same below). Introducing a group along x i Orthogonal reference coordinate vector b for direction i , the position of any point on the plate before deformation can be from fixed point O to x α Determine the position vector of the point describe:
[0026] r ^ ( x 1 , ...
PUM
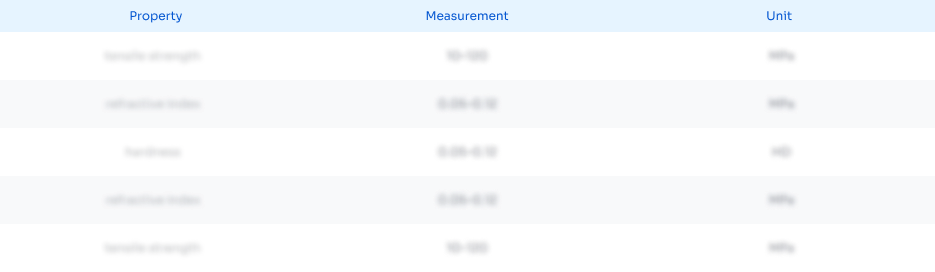
Abstract
Description
Claims
Application Information

- Generate Ideas
- Intellectual Property
- Life Sciences
- Materials
- Tech Scout
- Unparalleled Data Quality
- Higher Quality Content
- 60% Fewer Hallucinations
Browse by: Latest US Patents, China's latest patents, Technical Efficacy Thesaurus, Application Domain, Technology Topic, Popular Technical Reports.
© 2025 PatSnap. All rights reserved.Legal|Privacy policy|Modern Slavery Act Transparency Statement|Sitemap|About US| Contact US: help@patsnap.com