All-around lubricating film pressure wireless monitoring method of liquid sliding bearing
A liquid sliding bearing and sliding bearing technology, applied in the field of wireless transmission technology, can solve the problems of large measurement error, large loss of signal accuracy, large interference, etc., to achieve convenient installation, solve the problem of unbalance, avoid interference and loss of signal accuracy. Effect
- Summary
- Abstract
- Description
- Claims
- Application Information
AI Technical Summary
Problems solved by technology
Method used
Image
Examples
Embodiment
[0050] For a certain type of water-lubricated rubber bearing (see Figure 8 ) under different rotational speeds and loads to carry out the actual measurement of the lubricating film pressure as an example, illustrating the validity of the test method of the present invention. According to the actual size of the sliding bearing and the shaft, the design such as Figure 9 test method shown. Static and transient loading forces are applied to the shaft by means of electromagnetic loading, and the pressure of the lubricating film of the water-lubricated rubber bearing is tested by an adjustable-speed motor within the speed range of 100 to 1500r / min to obtain a set of lubricating films under different conditions pressure distribution curve. In addition, changing the water supply pressure and water supply temperature of the water-lubricated bearing, changing the working conditions of the bearing-rotor system according to the above speed and loading mode, and obtaining another set o...
PUM
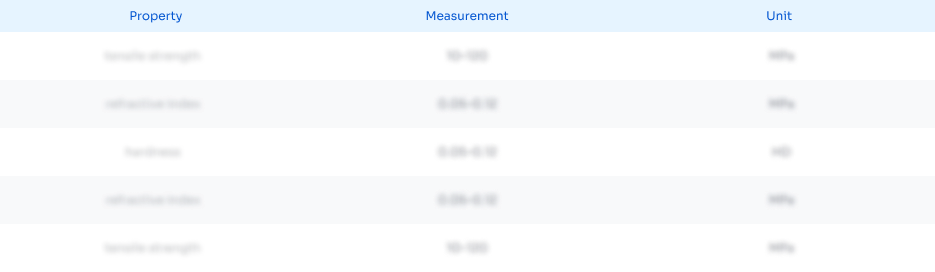
Abstract
Description
Claims
Application Information

- R&D
- Intellectual Property
- Life Sciences
- Materials
- Tech Scout
- Unparalleled Data Quality
- Higher Quality Content
- 60% Fewer Hallucinations
Browse by: Latest US Patents, China's latest patents, Technical Efficacy Thesaurus, Application Domain, Technology Topic, Popular Technical Reports.
© 2025 PatSnap. All rights reserved.Legal|Privacy policy|Modern Slavery Act Transparency Statement|Sitemap|About US| Contact US: help@patsnap.com