Decompression discharge pipe and raw material mixing system adopting the same
A batching system and feeding pipe technology, which is applied in the direction of conveying bulk materials, conveyors, transportation and packaging, etc., can solve the problems of raw material weighing errors, the inlet valve body of the mixing tank can not be completely sealed, leakage, etc.
- Summary
- Abstract
- Description
- Claims
- Application Information
AI Technical Summary
Problems solved by technology
Method used
Image
Examples
Embodiment 1
[0025] figure 1 It is a specific embodiment of a pressure relief type feed pipe. Among the figure, the large-scale outlet valve 8 and the mixing tank inlet valve 9 are respectively connected with the upper and lower parts of the feeding pipe body 19 with screws, and the feeding pipe body 19 is a cylinder or a square cylinder. An oblique upward pressure relief pipe 2 is installed on the side of the pipe body 19, and is welded and fixed at an angle of 45° with the blanking pipe body 19. A non-return air pipe 6 with an inner diameter of 10 mm is vertically installed on the pressure relief pipe 2 upper side at a distance of 200 mm from the discharge pipe body 19 along the pressure relief pipe 2 direction. The upper end of the pressure relief pipe 2 is connected to one end of a closed valve 3, and the other end of the closed valve 3 is connected to a transparent hose 4 with a length of 2 meters and a diameter of 60 mm. The transparent hose 4 is supported by an auxiliary bracket ne...
Embodiment 2
[0032] figure 2 It is a specific embodiment of the second pressure relief type feeding pipe. In the figure, the large scale outlet valve 8 and the mixing tank inlet valve 9 are respectively connected with the feeding pipe body 19 with screws, and the feeding pipe body 19 is a cylinder Body or square cylinder, a circular openable observation hole 1 with a diameter of 250 mm to 400 mm is set on the feeding pipe body 19 . An oblique upward pressure relief pipe 2 is installed on the blanking tube body 19 next to the observation hole 1, and is welded and fixed with the blanking tube body 19 at an angle of 30°. On the pressure relief pipe 2 upper side, along the direction of the pressure relief pipe 2, two check pipes 6 with an inner diameter of 5mm are installed in parallel at a distance of 200mm from the blanking pipe body 19 at a distance of 50mm. The upper end of the pressure relief pipe 2 is connected to one end of a closed valve 3, and the other end of the closed valve 3 is ...
Embodiment 3
[0038] image 3 It is a specific embodiment of the third pressure relief type feeding pipe. In the figure, the large scale outlet valve 8 and the mixing tank inlet valve 9 are respectively connected with the feeding pipe body 19 with screws, and the feeding pipe body 19 is a cylinder Two different openable observation holes 1 are set on the tube body 19 of the feeding pipe, which are respectively a large rectangular observation hole 1 of 250mm×400mm and a small circular observation hole of 2mm to 10mm. 15, and symmetrically or asymmetrically arranged in the horizontal direction of the feeding pipe body 19. An obliquely upward pressure relief pipe 2 is installed on the blanking tube body 19 next to the observation hole 1, and is welded and fixed with the blanking tube body 19 at an angle of 60°. On the pressure relief pipe 2 upper side, along the direction of the pressure relief pipe 2, a distance of 100mm and 200mm from the blanking pipe body 19 is vertically installed with t...
PUM
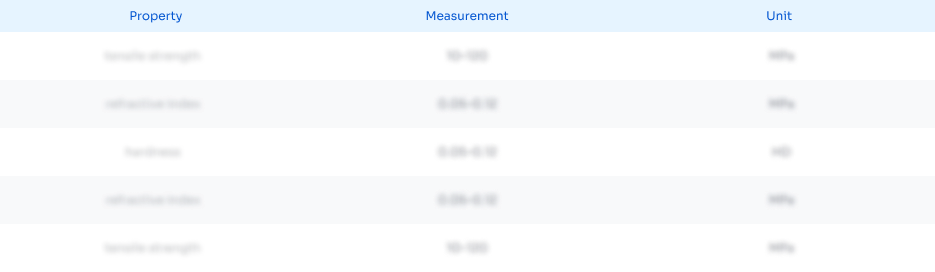
Abstract
Description
Claims
Application Information

- Generate Ideas
- Intellectual Property
- Life Sciences
- Materials
- Tech Scout
- Unparalleled Data Quality
- Higher Quality Content
- 60% Fewer Hallucinations
Browse by: Latest US Patents, China's latest patents, Technical Efficacy Thesaurus, Application Domain, Technology Topic, Popular Technical Reports.
© 2025 PatSnap. All rights reserved.Legal|Privacy policy|Modern Slavery Act Transparency Statement|Sitemap|About US| Contact US: help@patsnap.com