Drive shaft assembly for a downhole motor
A technology of drive shafts and components, applied in the field of universal joints, can solve problems such as difficult thrust loads, and achieve the effect of increasing torque load capacity and axial thrust load capacity
- Summary
- Abstract
- Description
- Claims
- Application Information
AI Technical Summary
Problems solved by technology
Method used
Image
Examples
Embodiment Construction
[0076] refer to figure 1 A drive shaft assembly 10 according to the present invention includes a drive shaft 20 having an upper end 22 and a lower end 24 , an upper end housing 30 and a lower end housing 40 . When assembled into a downhole motor, the drive shaft assembly 10 will be enclosed by a figure 1 In the tubular propshaft housing conceptually shown by dashed line 15 , an annular space 16 is formed between the propshaft housing 15 and the propeller shaft assembly 10 .
[0077] The upper housing 30 has a connector portion 32 adapted to be connected to an output shaft (not shown) of a power section of a downhole motor and a coaxially adjacent socket portion 34 adapted to To receive the upper end 22 of the propeller shaft 20 and accommodate the omnidirectional rotation of the propeller shaft 20 therein, while transmitting rotational torque and axial thrust loads from the output shaft to the propeller shaft 20 . The lower end housing 40 has a connector portion 42 adapted t...
PUM
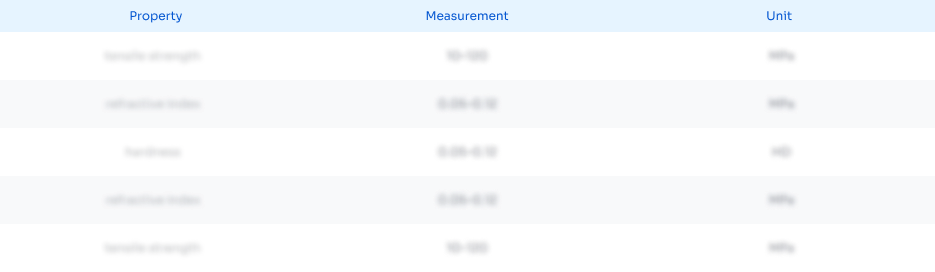
Abstract
Description
Claims
Application Information

- Generate Ideas
- Intellectual Property
- Life Sciences
- Materials
- Tech Scout
- Unparalleled Data Quality
- Higher Quality Content
- 60% Fewer Hallucinations
Browse by: Latest US Patents, China's latest patents, Technical Efficacy Thesaurus, Application Domain, Technology Topic, Popular Technical Reports.
© 2025 PatSnap. All rights reserved.Legal|Privacy policy|Modern Slavery Act Transparency Statement|Sitemap|About US| Contact US: help@patsnap.com