Spatial six-degree-of-freedom motion platform modal control method
A modal control, motion table technology, applied in non-electric variable control, vehicle position/route/height control, position/direction control, etc., can solve the problem of not being able to essentially improve and improve the control performance of a six-degree-of-freedom hydraulic motion table , the ambiguity of the corresponding relationship, the neglect of strong dynamic coupling characteristics, etc., to achieve the effect of improving the reproduction of single-degree-of-freedom motion and multi-degree-of-freedom compound motion, weakening the coupling effect, and increasing the bandwidth of the degree of freedom
- Summary
- Abstract
- Description
- Claims
- Application Information
AI Technical Summary
Problems solved by technology
Method used
Image
Examples
Embodiment 1
[0015] Example 1: Combining figure 1 , a modal control method for a space six-degree-of-freedom motion platform of the present invention, the steps are as follows:
[0016] Step 1: Use the modal matrix of the six-degree-of-space hydraulic motion table to transform the physical space system into the modal space, and construct a six-degree-of-freedom uncoupled hydraulic motion table in the modal space, that is, the spool of the hydraulic motion table in the physical space The input signal is converted into a modal spool input signal, and the hydraulic cylinder displacement output by the motion table or the output pose physical quantity after positive solution is transformed into a modal displacement or modal pose output signal. After the transformation from the physical space to the modal space, the space The six-degree-of-freedom hydraulic motion table is transformed into a mechanically coupled motion system, which is the key to the realization of the modal decoupling control t...
Embodiment 2
[0022] Example 2: Combining figure 1 , figure 1 It is a composition diagram of a six-degree-of-freedom motion platform. In the figure: (1) motion platform, (2) upper connecting hinge, (3) piston rod, (4) hydraulic cylinder, (5) lower connecting hinge, (6) base platform .
[0023] The total stroke of the hydraulic cylinder is 0.74m, and the length of the hydraulic cylinder in the middle position is 1.83m. The generalized pose expected by the motion platform is a 6-dimensional vector sx des , the expected displacement of the hydraulic cylinder relative to the median is a 6-dimensional vector l des , the spool driving voltage signal input by the motion table is a 6-dimensional vector V e , the actual output hydraulic cylinder displacement signal of the motion table is a 6-dimensional vector l.
[0024] There is a strong coupling between the hydraulic cylinders and degrees of freedom of the six-degree-of-freedom hydraulic motion table in space, and there is a coupling effect ...
Embodiment 3
[0025] Example 3: Binding figure 2 , the reference input signals in the signal generator in this example include constant value pose input signal, sinusoidal pose input signal and random pose input signal. The kinematics inverse solution module analyzes and calculates the 6-dimensional hydraulic cylinder displacement signal of the motion table corresponding to the given reference pose input signal according to the geometric principle des . The modal controller will expect the physical input displacement signal l des Transform the actual output physical displacement signal l of the six-degree-of-freedom hydraulic motion table into a modal signal Control, and then inversely transform the output modal spool displacement signal to the physical space to drive the servo valve to realize the drive and control of the motion table. The modal matrix used in the controller is:
[0026] U = 0.088 ...
PUM
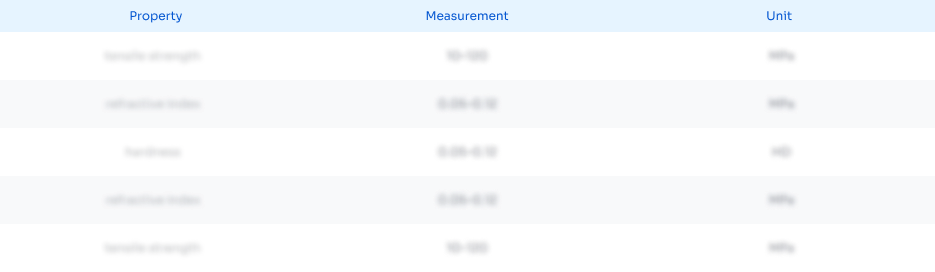
Abstract
Description
Claims
Application Information

- R&D Engineer
- R&D Manager
- IP Professional
- Industry Leading Data Capabilities
- Powerful AI technology
- Patent DNA Extraction
Browse by: Latest US Patents, China's latest patents, Technical Efficacy Thesaurus, Application Domain, Technology Topic, Popular Technical Reports.
© 2024 PatSnap. All rights reserved.Legal|Privacy policy|Modern Slavery Act Transparency Statement|Sitemap|About US| Contact US: help@patsnap.com