Controller for automatic transmission
A technology for automatic transmissions and control devices, applied in the direction of transmission control, elements with teeth, belts/chains/gears, etc., can solve damage to operational flexibility, reduce fuel consumption and operational flexibility, lack of realizability And other issues
- Summary
- Abstract
- Description
- Claims
- Application Information
AI Technical Summary
Problems solved by technology
Method used
Image
Examples
no. 2 approach
[0171] Next, follow Figure 26 and Figure 27 , and a second embodiment in which the above-mentioned first embodiment is partially modified will be described. In this second embodiment, compared with the first embodiment described above, the values in the downshift determination and the upshift determination determined by the downshift determination means 51 and the upshift determination means 52 are changed.
[0172] That is, in the above-mentioned first embodiment, the current gear ratio maximum power n_MAXpwr is used as a reference when determining a downshift, and the maximum power after upshifting n+_MAXpwr is used as a reference when determining an upshift. However, in the second embodiment In the mode, a value obtained by subtracting the surplus power E / G_reserved_pwr (drive source surplus output) capable of accelerating the rotation of the engine 2 is used from the above-mentioned value.
[0173]Therefore, in the downshift judgment of the second embodiment, the val...
no. 3 approach
[0191] Next, follow Figure 28 and Figure 29 , and a third embodiment in which the above-mentioned second embodiment is partially modified will be described. Compared with the second embodiment described above, this third embodiment further changes the values in the downshift determination and upshift determination determined by the downshift determination unit 51 and the upshift determination unit 52 .
[0192] That is, in the above-mentioned second embodiment, the larger value of the value obtained by adding the balance power balanced_pwr to the remaining output reserved_pwr and the requested power req_pwr is used as the first value when making a downshift judgment, and when making an upshift judgment, set The value obtained by adding the balanced power balanced_pwr to the remaining output reserved_pwr, the value obtained by adding the larger one of the required power req_pwr plus the hysteresis power hys_pwr is used as the third value, and in this third embodiment, the ...
no. 4 approach
[0211] Next, follow Figure 30 and Figure 31 A fourth embodiment partially modified from the first embodiment described above will be described. In this fourth embodiment, the calculation method of the remaining output reserved_pwr is changed compared to the first embodiment described above.
[0212] The remaining output calculation unit 31' of the fourth embodiment switches between the normal (Normal) mode, the economical (ECO) mode, and the sport (Sport) mode based on the required excess amount over_pwr obtained by subtracting the balanced power balanced_pwr from the required power req_pwr and the accelerator opening θd. For these three modes, a value corresponding to each mode is used as the remaining output reserved_pwr.
[0213] In detail, for example, during running in the normal mode, when the remaining output calculation unit 31' judges (five times) that the accelerator pedal is depressed and the required excess amount over_pwr is below the first threshold a1 (eg, 1...
PUM
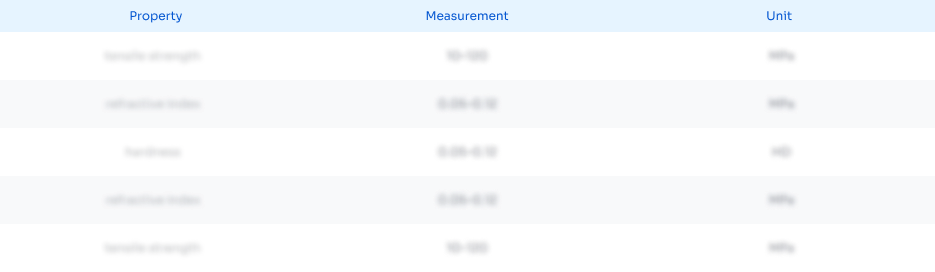
Abstract
Description
Claims
Application Information

- Generate Ideas
- Intellectual Property
- Life Sciences
- Materials
- Tech Scout
- Unparalleled Data Quality
- Higher Quality Content
- 60% Fewer Hallucinations
Browse by: Latest US Patents, China's latest patents, Technical Efficacy Thesaurus, Application Domain, Technology Topic, Popular Technical Reports.
© 2025 PatSnap. All rights reserved.Legal|Privacy policy|Modern Slavery Act Transparency Statement|Sitemap|About US| Contact US: help@patsnap.com