An energy recovery system for a vehicle driveline
A kinetic energy recovery system and transmission system technology, applied in the field of kinetic energy recovery systems, can solve problems such as small expected range
- Summary
- Abstract
- Description
- Claims
- Application Information
AI Technical Summary
Problems solved by technology
Method used
Image
Examples
Embodiment Construction
[0019] figure 1 The engine 10 shown is in the present embodiment an internal combustion engine, although in principle the invention could be implemented using another type of rotary drive. The drivetrain shown is intended for use in a motor vehicle, but can also be applied to other types of vehicles, such as trains. figure 1 The dashed box 12 in contains what is representative of any motor vehicle driveline. In the figure, the transmission of the vehicle, which is used to transmit rotational drive from the engine 10 to the driven wheels of the vehicle, is represented by box 14 (which is the transmission input) and circle 16 (which represents the speed ratio of the transmission) (not shown). The transmission may be of any suitable type and may provide stepped or continuously variable gear ratios. The driving force transmitted to the wheels acts on the vehicle inertia 18 to accelerate / decelerate it. In this example, the first clutch 20 is used to selectively disengage the tr...
PUM
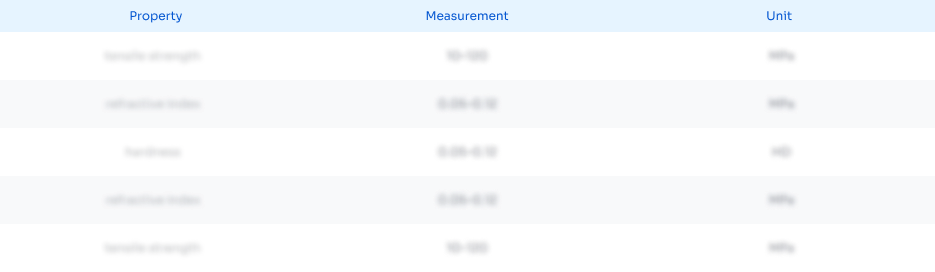
Abstract
Description
Claims
Application Information

- Generate Ideas
- Intellectual Property
- Life Sciences
- Materials
- Tech Scout
- Unparalleled Data Quality
- Higher Quality Content
- 60% Fewer Hallucinations
Browse by: Latest US Patents, China's latest patents, Technical Efficacy Thesaurus, Application Domain, Technology Topic, Popular Technical Reports.
© 2025 PatSnap. All rights reserved.Legal|Privacy policy|Modern Slavery Act Transparency Statement|Sitemap|About US| Contact US: help@patsnap.com