Multi-camera system calibrating method based on optical imaging test head and visual graph structure
An optical imaging, multi-camera technology, applied in the field of visual measurement, can solve the problems of initial parameter error, low efficiency, low precision, etc.
- Summary
- Abstract
- Description
- Claims
- Application Information
AI Technical Summary
Problems solved by technology
Method used
Image
Examples
Embodiment Construction
[0069] The present invention will be further described below in conjunction with accompanying drawing.
[0070] Take the vision system composed of 8 cameras as an example for specific description. The present invention uses as figure 1 Optical imaging probe shown. The optical imaging probe is mainly composed of a measuring tip (2), an extension rod (3), a target body (4), 7 mark points (5) and LED light spots thereof. The distribution of 8 cameras is as follows image 3 As shown, all cameras are not required to have overlapping fields of view, but at least every two cameras have overlapping fields of view. According to the spatial distribution of 8 cameras, the method first selects and determines the spatial positioning points, and uses the rotation invariant relationship of the optical imaging probe around the measuring tip to complete the independent calibration of a single camera and the relative pose calibration of every two cameras. Then, the multi-camera connection r...
PUM
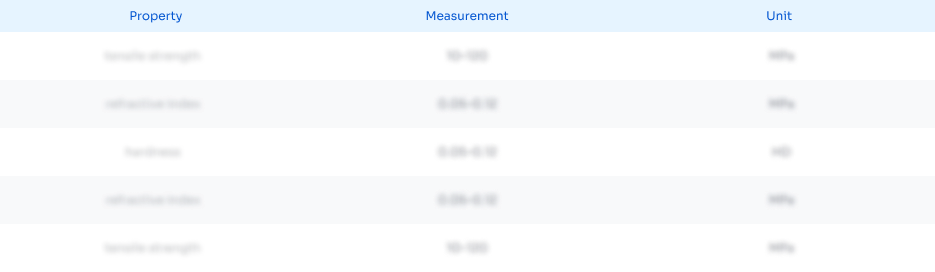
Abstract
Description
Claims
Application Information

- R&D
- Intellectual Property
- Life Sciences
- Materials
- Tech Scout
- Unparalleled Data Quality
- Higher Quality Content
- 60% Fewer Hallucinations
Browse by: Latest US Patents, China's latest patents, Technical Efficacy Thesaurus, Application Domain, Technology Topic, Popular Technical Reports.
© 2025 PatSnap. All rights reserved.Legal|Privacy policy|Modern Slavery Act Transparency Statement|Sitemap|About US| Contact US: help@patsnap.com