Production process for straw coal
A production process and straw coal technology, applied in the field of biomass renewable energy manufacturing, can solve the problems of coal-fired boilers that do not meet environmental protection requirements, heavy operating pressure of enterprises, and atmospheric environmental pollution, and achieve good quality, long burning time, and improved environment. Effect
- Summary
- Abstract
- Description
- Claims
- Application Information
AI Technical Summary
Problems solved by technology
Method used
Examples
Embodiment 1
[0008] Embodiment 1 A kind of production technology of straw coal
[0009] Crush the straw; put the crushed straw into the carbonization furnace, and carbonize at 800-1200°C for 30-50 minutes under anaerobic condition; cool down to 200-250°C, add loess, coal slime, sulfur fixative and Paraffin wax, the proportion by weight is: 100 parts of carbonized straw, 25 parts of loess, 25 parts of coal slime, 0.5 part of sulfur-fixing agent, and 0.5 part of paraffin wax. The materials are mixed evenly; sent into an extruder, shaped and dried.
Embodiment 2
[0010] Embodiment 2 A kind of production technology of straw coal
[0011] Crush the straw; put the crushed straw into the carbonization furnace, and carbonize at 800-1200°C for 30-50 minutes under anaerobic condition; cool down to 200-250°C, add loess, coal slime, sulfur fixative and Paraffin wax, the proportion by weight is: 100 parts of carbonized straw, 20 parts of loess, 20 parts of coal slime, 0.1 part of sulfur-fixing agent, and 0.1 part of paraffin wax. The materials are mixed evenly; sent into an extruder, shaped and dried.
Embodiment 3
[0012] Embodiment 3 A kind of production technology of straw coal
[0013] Crush the straw; put the crushed straw into the carbonization furnace, and carbonize at 800-1200°C for 30-50 minutes under anaerobic condition; cool down to 200-250°C, add loess, coal slime, sulfur fixative and Paraffin wax, the proportion by weight is: 100 parts of carbonized straw, 30 parts of loess, 30 parts of coal slime, 0.7 part of sulfur-fixing agent, and 0.7 part of paraffin wax. The materials are mixed evenly; sent into an extruder, shaped and dried.
PUM
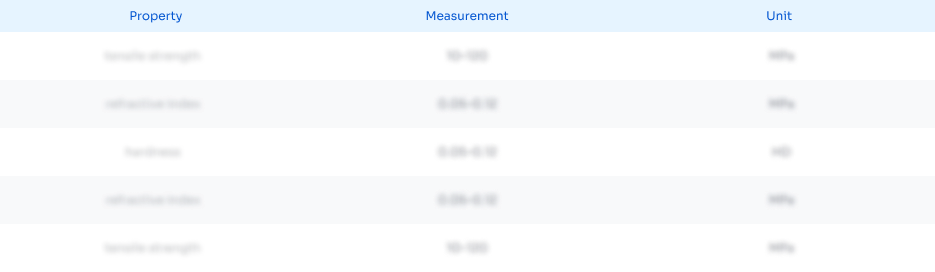
Abstract
Description
Claims
Application Information

- R&D
- Intellectual Property
- Life Sciences
- Materials
- Tech Scout
- Unparalleled Data Quality
- Higher Quality Content
- 60% Fewer Hallucinations
Browse by: Latest US Patents, China's latest patents, Technical Efficacy Thesaurus, Application Domain, Technology Topic, Popular Technical Reports.
© 2025 PatSnap. All rights reserved.Legal|Privacy policy|Modern Slavery Act Transparency Statement|Sitemap|About US| Contact US: help@patsnap.com