Method for compensating frictional error of servo system of numerical control machine tool
A friction error and friction compensation technology, which is applied in the field of friction error compensation for CNC machine tool servo systems, can solve the problems of limited compensation effect, strong changes in friction force, and short action time, and achieve the effect of realizing friction error compensation and shortening output.
- Summary
- Abstract
- Description
- Claims
- Application Information
AI Technical Summary
Problems solved by technology
Method used
Image
Examples
Embodiment Construction
[0025] The friction error compensation method of the CNC machine tool servo control system of the present invention comprises the following steps:
[0026] 1) First, the position interpolator 2 outputs a position command to the differential device, and the differential device calculates an input signal of a speed command according to the position command, and transmits it to the friction command generator 1;
[0027] 2) The friction command generator 1 calculates and generates the friction compensation command signal C according to the speed command input signal r ;
[0028] 3) The friction compensator 3 according to the friction compensation instruction signal C r The friction compensation value signal is calculated, and then the friction compensation value signal output by the friction compensator 3 is maintained by the first zero-order holder 5 under the sampling period determined by the first timer 7. The first zero-order holder 5 output feedforward compensation signal u...
PUM
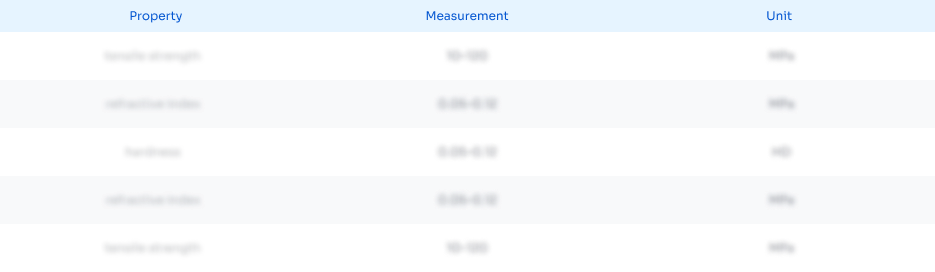
Abstract
Description
Claims
Application Information

- R&D
- Intellectual Property
- Life Sciences
- Materials
- Tech Scout
- Unparalleled Data Quality
- Higher Quality Content
- 60% Fewer Hallucinations
Browse by: Latest US Patents, China's latest patents, Technical Efficacy Thesaurus, Application Domain, Technology Topic, Popular Technical Reports.
© 2025 PatSnap. All rights reserved.Legal|Privacy policy|Modern Slavery Act Transparency Statement|Sitemap|About US| Contact US: help@patsnap.com