Electromechanical coupling vibration test device for maglev train
A technology of electromechanical coupling and vibration testing, which is applied in vibration testing, measuring devices, and fluids using vibration, etc., can solve the problems of increased construction costs, too simple research, and lack of pertinence, and achieves simple structure, good simulation effect, and self-weight light effect
- Summary
- Abstract
- Description
- Claims
- Application Information
AI Technical Summary
Problems solved by technology
Method used
Image
Examples
Embodiment Construction
[0017] The present invention is described in further detail now in conjunction with accompanying drawing. These drawings are all simplified schematic diagrams, which only illustrate the basic structure of the present invention in a schematic manner, so they only show the configurations related to the present invention.
[0018] Take the F rail of the low-speed maglev train, the 14-point hydraulic support of the first-level platform, and the maximum 4×5 steel spring supports of the second-level platform 2 as an example.
[0019] Such as figure 1 , figure 2 , image 3 A maglev train electromechanical coupling vibration test device shown mainly consists of a hydraulic excitation system 4, a first-level platform 1 that simulates ground support, and a second-level platform 2 that simulates the quality of the track beam above the first-level platform 1. The track beam stiffness adjustment system 3 composed of adjusted steel springs and the horizontal displacement prevention auxi...
PUM
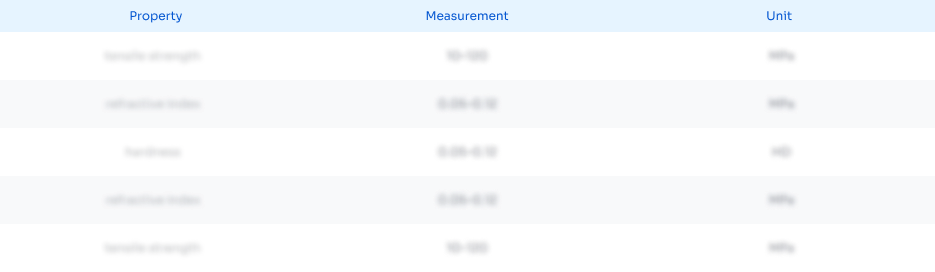
Abstract
Description
Claims
Application Information

- R&D
- Intellectual Property
- Life Sciences
- Materials
- Tech Scout
- Unparalleled Data Quality
- Higher Quality Content
- 60% Fewer Hallucinations
Browse by: Latest US Patents, China's latest patents, Technical Efficacy Thesaurus, Application Domain, Technology Topic, Popular Technical Reports.
© 2025 PatSnap. All rights reserved.Legal|Privacy policy|Modern Slavery Act Transparency Statement|Sitemap|About US| Contact US: help@patsnap.com