Adaptive control of composite plycutting
An automatic controller and layer-laying technology, applied in thin material processing, metal processing, transportation and packaging, etc., can solve the problem of not using CNC ultrasonic cutting machine, etc., and achieve the effect of reducing the amount of programming
- Summary
- Abstract
- Description
- Claims
- Application Information
AI Technical Summary
Problems solved by technology
Method used
Image
Examples
Embodiment Construction
[0019] first reference figure 1 , which shows a system 10 for cutting a plurality of plies 14 of composite material using an automatically controlled ultrasonic cutter generally indicated by the numeral 12 . Although multiple plies 14 of composite material are shown in connection with the disclosed embodiments, it should be understood that individual plies of composite material as well as materials other than composite material may be cut. The layups may be raw (uncured) where the cutter 12 is used to cut the shape of the layups used to form the layups during the initial fabrication of the structure. However, embodiments of the present invention may also be used to cut partially or fully cured layups after a structure has been fabricated, such as during repair of composite aircraft components or subassemblies where a portion of the component / subassembly must be cut away.
[0020] The ultrasonic cutter 12 is mounted on a toolhead 16 that is movable along a plurality of machine...
PUM
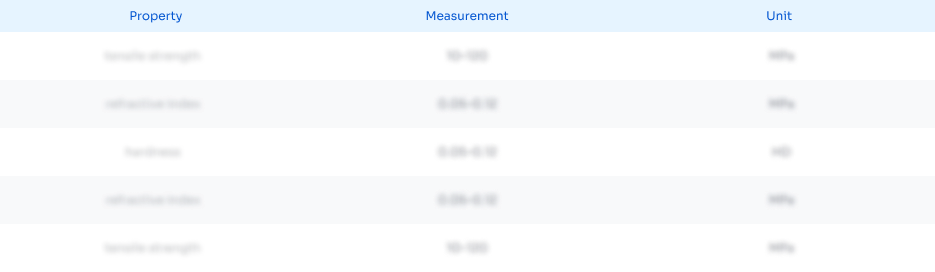
Abstract
Description
Claims
Application Information

- R&D Engineer
- R&D Manager
- IP Professional
- Industry Leading Data Capabilities
- Powerful AI technology
- Patent DNA Extraction
Browse by: Latest US Patents, China's latest patents, Technical Efficacy Thesaurus, Application Domain, Technology Topic, Popular Technical Reports.
© 2024 PatSnap. All rights reserved.Legal|Privacy policy|Modern Slavery Act Transparency Statement|Sitemap|About US| Contact US: help@patsnap.com