Multiaxial artificial joints tester
An artificial joint and testing machine technology, which is applied in the direction of testing wear resistance, etc., can solve the problems that the actual movement mode of the human hip joint is quite different, the artificial hip joint simulation testing machine has not yet been seen, and the structure is complex. Prevent leakage, good simulation effect
- Summary
- Abstract
- Description
- Claims
- Application Information
AI Technical Summary
Problems solved by technology
Method used
Image
Examples
Embodiment Construction
[0011] An embodiment of the present invention will be further described below in conjunction with accompanying drawing:
[0012] figure 1 As shown, the multi-axis artificial joint testing machine of the present invention is mainly composed of a frame-shaped support, an electric cylinder 3, a center support 23, a solution basin 18, a moving platform 7, an upper ball hinge 6, and a lower ball hinge 24. The frame-shaped support includes The top plate 8, the base plate 1 corresponding to the top plate 8, and a pillar 9 for fixing it as a whole by bolts is arranged between the top and bottom plates. The bottom plate 1 middle part of the frame-shaped support is fixed with a central support 23 through screws, and three reinforcing ribs are evenly arranged on the outside of the central support 23 in the longitudinal direction. There is a spherical base 22 matching its arc surface, and the middle part of the arc seat ring 4 has a through hole that helps the disassembly of the spherica...
PUM
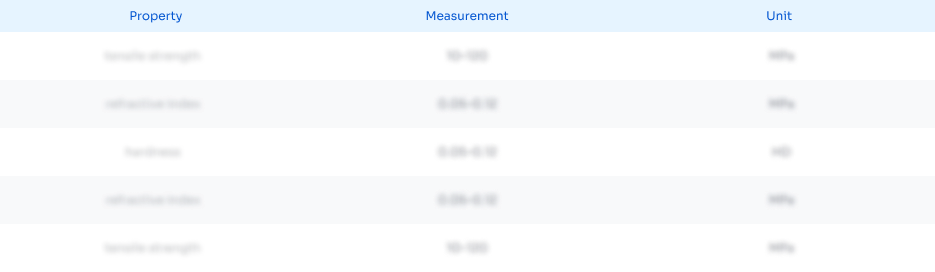
Abstract
Description
Claims
Application Information

- R&D
- Intellectual Property
- Life Sciences
- Materials
- Tech Scout
- Unparalleled Data Quality
- Higher Quality Content
- 60% Fewer Hallucinations
Browse by: Latest US Patents, China's latest patents, Technical Efficacy Thesaurus, Application Domain, Technology Topic, Popular Technical Reports.
© 2025 PatSnap. All rights reserved.Legal|Privacy policy|Modern Slavery Act Transparency Statement|Sitemap|About US| Contact US: help@patsnap.com