Integrally molded fiber microsensor and manufacturing method thereof
A micro-sensor and optical fiber technology, which is applied in the use of optical devices to transmit sensing components, light guides, optics, etc., can solve the problems of being susceptible to external interference, poor stability of planar waveguide-coupled optical fiber sensors, and complex fabrication, and to overcome instability. , the effect of simple structure and high coupling efficiency
- Summary
- Abstract
- Description
- Claims
- Application Information
AI Technical Summary
Problems solved by technology
Method used
Image
Examples
Embodiment Construction
[0022] In order to better illustrate the purpose and advantages of the present invention, the technical solutions of the present invention will be further described below in conjunction with the accompanying drawings and specific embodiments.
[0023] figure 1 It is a schematic diagram of the overall structure of the integrally formed microsensor in this specific embodiment. In this embodiment, Corning's SMF-28e optical fiber is selected, and a groove with a length of 75 microns and a depth of 58 microns is processed on the upper side of any part thereof, and the bottom surface of the groove as a sensing structure is uniformly increased in refractive index. Large flat TLC.
[0024] The specific preparation process of the microsensor of the present embodiment is:
[0025] Step 1, design the length of the fiber groove according to the test requirements;
[0026] Step 2, take a SMF-28e optical fiber 3, remove a section of optical fiber coating layer on the desired part of the ...
PUM
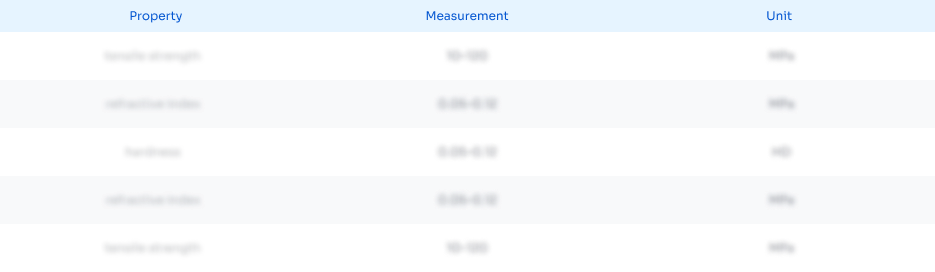
Abstract
Description
Claims
Application Information

- Generate Ideas
- Intellectual Property
- Life Sciences
- Materials
- Tech Scout
- Unparalleled Data Quality
- Higher Quality Content
- 60% Fewer Hallucinations
Browse by: Latest US Patents, China's latest patents, Technical Efficacy Thesaurus, Application Domain, Technology Topic, Popular Technical Reports.
© 2025 PatSnap. All rights reserved.Legal|Privacy policy|Modern Slavery Act Transparency Statement|Sitemap|About US| Contact US: help@patsnap.com