Flash butt welding machine for vehicle door corner welding
A butt welding machine and corner technology, applied in welding equipment, resistance welding equipment, metal processing equipment, etc., can solve the problems of lack of flexible adjustment and quick replacement, and inability to well adapt to the special requirements of the corner welding of automobile door frames. To achieve the effect of labor-saving installation, convenient adjustment and flexible adjustment
- Summary
- Abstract
- Description
- Claims
- Application Information
AI Technical Summary
Problems solved by technology
Method used
Image
Examples
Embodiment Construction
[0047] The present invention will be further described in detail below in conjunction with the accompanying drawings and embodiments.
[0048] Such as Figure 1 to Figure 10 As shown, the butt welding machine of this embodiment is mainly used for the welding of the corners of the automobile door frame formed by the products at both ends. Usually, the welding end faces of the corner profiles of the automobile door frame are produced by oblique sawing of the products, and the end faces of the two sides of the products to be welded The cross-section difference must meet the cross-section conditions for flash-butt welding of door frame profiles, and the cross-section difference is generally required to be within 10%.
[0049] The butt welding machine of this embodiment includes
[0050] The machine base 1, the machine base 1 can be used as an electric control box, electric control equipment such as PLC is placed in the machine base 1, and a clamp base plate 6 is fixed on the mach...
PUM
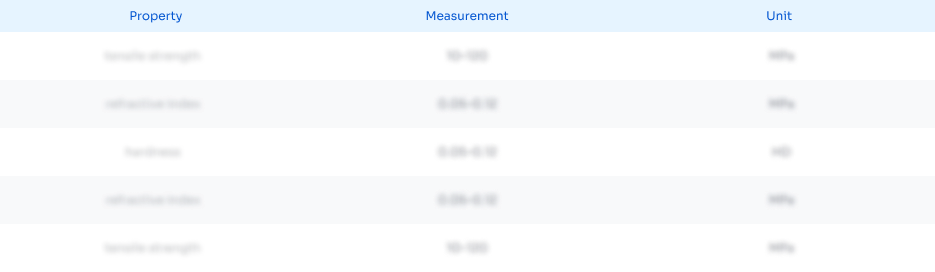
Abstract
Description
Claims
Application Information

- R&D
- Intellectual Property
- Life Sciences
- Materials
- Tech Scout
- Unparalleled Data Quality
- Higher Quality Content
- 60% Fewer Hallucinations
Browse by: Latest US Patents, China's latest patents, Technical Efficacy Thesaurus, Application Domain, Technology Topic, Popular Technical Reports.
© 2025 PatSnap. All rights reserved.Legal|Privacy policy|Modern Slavery Act Transparency Statement|Sitemap|About US| Contact US: help@patsnap.com