Method for preparing copper-lead alloy/steel bimetal laminated composite material
A technology of bimetallic layered and composite materials, which is applied in the field of preparation of copper-lead alloy/steel bimetallic layered composite materials, can solve problems such as copper-lead alloy structure segregation, and achieve low production cost, low cost, equipment and technology simple effect
- Summary
- Abstract
- Description
- Claims
- Application Information
AI Technical Summary
Problems solved by technology
Method used
Image
Examples
Embodiment 1
[0037] Choose ordinary steel plate, wash ordinary steel plate in 10% NaOH solution at 80°C for 2 minutes to remove oil; wash in 10% hydrochloric acid for 2 minutes to remove rust; 2 CO 3 Rinse in medium for 1 minute to neutralize residual acid, rinse with clean water, preheat the steel plate to 150°C in a box-type resistance furnace, and then brush a layer of saturated ZnCl on the surface of the steel plate 2 After the solution is preheated to 200°C to obtain a rigid matrix for use; according to the mass percentage, weigh 1% charcoal, 67.9% electrolytic copper, 1% tin, 30% lead, and 0.1% phosphor copper. Put charcoal into the induction furnace, then put electrolytic copper, heat until the copper is melted, add tin and lead, after the alloy is mixed evenly, add phosphorus copper to deoxidize the alloy; pre-heat the graphite mold with chilling effect in the box-type resistance furnace Heat to 600°C, tool the preheated graphite mold and steel substrate, and transfer the copper-l...
Embodiment 2
[0039]Choose common steel plate, clean the steel plate in 10% NaOH solution at 85°C for 3 minutes to remove oil; wash in 10% hydrochloric acid for 5 minutes to remove rust; 2 CO 3 Rinse in medium for 2 minutes to neutralize residual acid, rinse with clean water, preheat the steel plate to 200°C in a box-type resistance furnace, and then brush a layer of saturated ZnCl on the surface of the steel plate 2 After the solution is preheated to 600°C to obtain a rigid matrix for use; according to the mass percentage, weigh 3% charcoal, 81.7% electrolytic copper, 5% tin, 10% lead, and 0.3% phosphor copper. Put charcoal into the induction furnace, then put electrolytic copper, heat until the copper is melted, add tin and lead, after the alloy is mixed evenly, add phosphorus copper to deoxidize the alloy; pre-heat the graphite mold with chilling effect in the box-type resistance furnace Heat to 600°C, tool the preheated graphite mold and steel matrix, and transfer the copper-lead alloy...
Embodiment 3
[0041] Select 20 steel plates, 20 steel plates are cleaned in 10% NaOH solution at 83°C for 2 minutes to remove oil; in 10% hydrochloric acid for 3 minutes to remove rust; in 10% NaOH solution 2 CO 3 Rinse in medium for 2 minutes to neutralize the residual acid, rinse with clean water, preheat the steel plate to 170°C in a box-type resistance furnace, and then brush a layer of saturated ZnCl on the surface of the steel plate 2 After the solution is preheated to 400°C to obtain a rigid matrix for use; according to the mass percentage, weigh 2% charcoal, 74% electrolytic copper, 3% tin, 20.8% lead, and 0.2% phosphor copper. Put charcoal into the induction furnace, then put electrolytic copper, heat until the copper is melted, add tin and lead, after the alloy is mixed evenly, add phosphorus copper to deoxidize the alloy; pre-heat the graphite mold with chilling effect in the box-type resistance furnace Heat to 600°C, tool the preheated graphite mold and steel matrix, and trans...
PUM
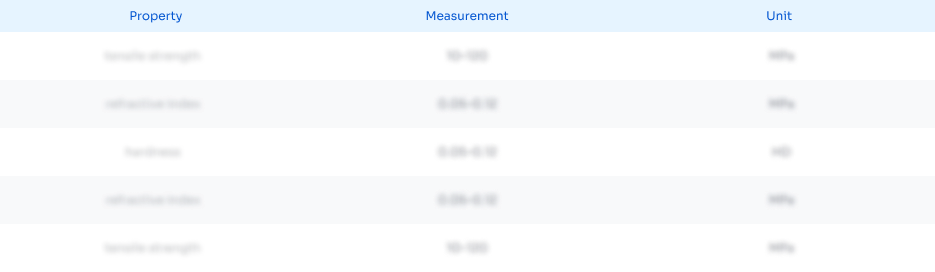
Abstract
Description
Claims
Application Information

- R&D
- Intellectual Property
- Life Sciences
- Materials
- Tech Scout
- Unparalleled Data Quality
- Higher Quality Content
- 60% Fewer Hallucinations
Browse by: Latest US Patents, China's latest patents, Technical Efficacy Thesaurus, Application Domain, Technology Topic, Popular Technical Reports.
© 2025 PatSnap. All rights reserved.Legal|Privacy policy|Modern Slavery Act Transparency Statement|Sitemap|About US| Contact US: help@patsnap.com