Micro-powder polishing brick
A technology for polishing tiles and micropowders, applied in the field of architectural tiles, can solve the problems of poor tone softness, poor three-dimensional effect and poor texture, and achieve the effects of soft tone, strong three-dimensional effect and good texture.
- Summary
- Abstract
- Description
- Claims
- Application Information
AI Technical Summary
Problems solved by technology
Method used
Image
Examples
Embodiment 1
[0010] ① Produce the base material according to the conventional process.
[0011] ②The following raw materials are prepared in parts by weight: washed ball soil 12, potassium sodium sand 30, albite feldspar 40, wurstite 10, aluminum sand 8. Grind fineness to 80 mesh or more and sieve 18-20%. Its chemical composition is calculated by weight percentage: SiO 2 67.04, Al 2 o 3 18.25, Fe 2 o 3 0.29, TiO 2 0.2, CaO 1.59, MgO 2.35, K 2 O 2.47, Na 2 O 4.95, IL 2.86.
[0012] ③Using the secondary cloth of the press, the pressure: 30000KN. During the firing process, the surface temperature of the kiln is controlled at 1175°C, the bottom temperature is controlled at 1200°C, and the firing cycle is 55 minutes.
[0013] The detection indexes of the products made in this embodiment are shown in Table 1.
[0014]
[0015] Radioactivity detection: Hebei Provincial Building Sanitary Ceramics Product Quality Supervision and Inspection Station, the inspection results: I(Ra) is...
Embodiment 2
[0017] ① Produce the base material according to the conventional process.
[0018] ②The following raw materials are prepared in parts by weight: washed ball soil 18, potassium sodium sand 24, albite feldspar 40, wurstite 10, aluminum sand 8. Grind fineness to 80 mesh or more and sieve 18-20%. Its chemical composition is SiO in weight percent 2 67.14, Al 2 o 3 18.52, Fe 2 o 3 0.26, TiO 2 0.14, CaO 1.52, MgO 2.45, K 2 O 2.20, Na 2 O 4.68, IL 3.04, and the balance is unanalyzed trace substances.
[0019] ③Using the secondary cloth of the press, the pressure: 31000KN. During the firing process, the surface temperature of the kiln is controlled at 1180°C, the bottom temperature is controlled at 1225°C, and the firing cycle is 45 minutes.
[0020] The detection indexes of the products made in this embodiment are shown in Table 1.
[0021]
[0022]
[0023] Radioactivity detection: Hebei Provincial Building Sanitary Ceramics Product Quality Supervision and Inspec...
Embodiment 3
[0025] ① Produce the base material according to the conventional process.
[0026] ②The following raw materials are prepared in parts by weight: washed ball soil 18, potassium sodium sand 30, albite feldspar 40, wurstite 4, aluminum sand 8. Grind fineness to 80 mesh or more and sieve 18-20%. Its chemical composition is SiO in weight percent 2 66.56, Al 2 o 3 19.75, Fe 2 o 3 0.28, TiO 2 0.16, CaO 0.96, MgO1.21, K 2 O 2.46, Na 2 O 4.94, IL 3.52, and the balance is unanalyzed trace substances.
[0027] ③Using the secondary cloth of the press, the pressure: 32000KN. During the firing process, the surface temperature of the kiln is controlled at 1178°C, the bottom temperature is controlled at 1210°C, and the firing cycle is 50 minutes.
[0028] The detection indexes of the products made in this embodiment are shown in Table 1.
[0029]
[0030] Radioactivity detection: Hebei Provincial Building Sanitary Ceramics Product Quality Supervision and Inspection Station, ...
PUM
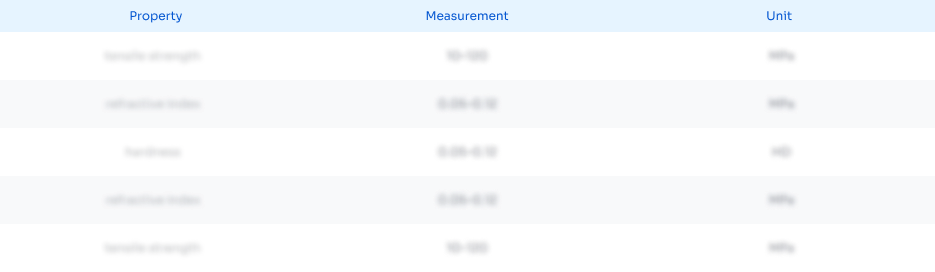
Abstract
Description
Claims
Application Information

- R&D
- Intellectual Property
- Life Sciences
- Materials
- Tech Scout
- Unparalleled Data Quality
- Higher Quality Content
- 60% Fewer Hallucinations
Browse by: Latest US Patents, China's latest patents, Technical Efficacy Thesaurus, Application Domain, Technology Topic, Popular Technical Reports.
© 2025 PatSnap. All rights reserved.Legal|Privacy policy|Modern Slavery Act Transparency Statement|Sitemap|About US| Contact US: help@patsnap.com