Self-adhesion membrane blowing production equipment and production method
A kind of production equipment and technology of self-adhesive film, which is applied in the production equipment and production field of self-adhesive film blowing method, which can solve the problems of self-adhesive film wrinkles, shaking, stickiness, and unwinding smoothly
- Summary
- Abstract
- Description
- Claims
- Application Information
AI Technical Summary
Problems solved by technology
Method used
Image
Examples
Embodiment 1
[0031] figure 1 , figure 2 , image 3 As shown, the self-adhesive film blown film production equipment includes a machine head 41, a herringbone splint 42, a film tube traction nip roller 6, a cutting knife 7, and two sets of film take-up mechanisms 81, 82 on the left and right, wherein the herringbone splint 42 Located above the machine head 41, the film tube traction nip roller 6 is located above the splint 42, and the left and right film coiling mechanisms 81, 82 are located below the cutting knife 7, and a pair of diaphragms are arranged below the cutting knife 7 Traction nip roller, the above-mentioned diaphragm traction nip roller comprises the first driving roller 11, the first driven roller 12, and the first driving roller 11, the first driven roller 12 are rubber rollers, the first driving roller 11 is formed by the first Driven by a motor; under the diaphragm traction nip roller, there are two pairs of split nip rollers symmetrically arranged left and right, and t...
Embodiment 2
[0038] In this embodiment, when the bracket moves to the upper end of the guide rail, the clearance distance between the splitting nip roller and the film traction nip roller is 10MM; and the angle formed between the line segment AB and the line segment CD is 60°. When the bracket moves to the lower end of the guide rail, the clearance distance between the splitting nip roller and the diaphragm traction nip roller is 400MM.
[0039] In addition, in the second embodiment, the first driving roller is a metal roller (left roller), and the first driven roller is a rubber roller (right roller). In each pair of splitting nip rollers, the second driving roller is a metal roller, the second driven roller is a silica gel roller, and the silica gel roller is located obliquely below the inner side of the metal roller.
[0040] All the other are the same as the first embodiment.
Embodiment 3
[0042] In this embodiment, when the bracket moves to the upper end of the guide rail, the clearance distance between the splitting nip roller and the film traction nip roller is 150 mm; and the angle formed between the line segment AB and the line segment CD is 178°. When the bracket moves to the lower end of the guide rail, the clearance distance between the splitting nip roller and the diaphragm traction nip roller is 850MM.
[0043] In addition, in the third embodiment, the first driving roller is a metal roller (right roller), and the first driven roller is a rubber roller (left roller). Both the second driving roller and the second driven roller are silicone rollers, one of which is located obliquely below the inner side of the other roller, the roller located obliquely below the inner side is the second driving roller, and the roller obliquely above the outer side is the second driven roller.
[0044] All the other are the same as the first embodiment.
PUM
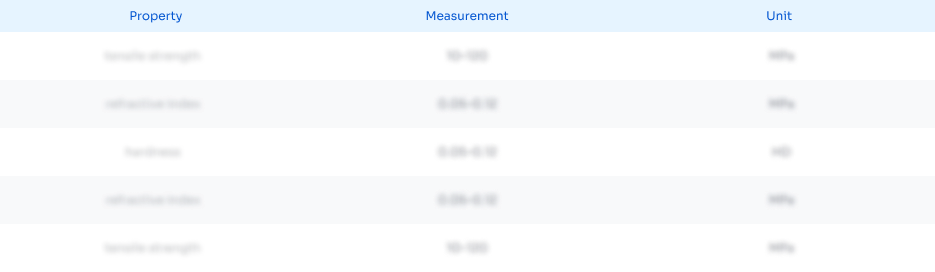
Abstract
Description
Claims
Application Information

- R&D
- Intellectual Property
- Life Sciences
- Materials
- Tech Scout
- Unparalleled Data Quality
- Higher Quality Content
- 60% Fewer Hallucinations
Browse by: Latest US Patents, China's latest patents, Technical Efficacy Thesaurus, Application Domain, Technology Topic, Popular Technical Reports.
© 2025 PatSnap. All rights reserved.Legal|Privacy policy|Modern Slavery Act Transparency Statement|Sitemap|About US| Contact US: help@patsnap.com