Method for producing nonyl phenol
- Summary
- Abstract
- Description
- Claims
- Application Information
AI Technical Summary
Problems solved by technology
Method used
Image
Examples
Embodiment 1
[0032] Such as figure 1 As shown, firstly, phenol and nonene as raw materials are sent to the deferrization column reactor to remove iron ions, and then the phenol is preheated to 115°C, and then the nonene and the preheated phenol are fully mixed, and the mixing ratio is Be phenol: nonene=1.8: 1, the mixed material enters the three-stage fixed-bed adiabatic reaction device that mainly is made up of three reactors successively, and the capacity of each reactor is the same, all is 6 cubic meters / piece, each stage reactors such as figure 2As shown, the top of the reactor is an inlet 1, and the bottom is a discharge valve 2. A sieve plate and a water tap 3 are arranged near the discharge valve 2, and 5 cubic alkylphenol special resin catalysts 4 are filled inside the reactor. It is the A36 type alkylphenol special resin catalyst produced by Rohm and Haas Company of the United States. Thermometers are installed in the upper, middle and lower sections of the reactor to monitor th...
Embodiment 2
[0034] like figure 1 As shown, firstly, phenol and nonene as raw materials are sent to the deferrization column reactor to remove iron ions, and then the phenol is preheated to 125°C, and then the nonene and the preheated phenol are fully mixed, and the mixing ratio is It is phenol: nonene=2.5: 1, and the mixed materials enter the three-stage fixed bed adiabatic reaction device successively, and each stage reactor is filled with 5 cubic alkylphenol special-purpose resin catalysts, and this catalyst is American Rohm and Haas Company The A36 type alkylphenol special resin catalyst produced. Wherein the input speed of the first stage reactor is 1.9 tons / hour, the feed temperature is 125°C, and the opening degree of the bottom valve control of the first stage reactor is 35%. The material after the first-stage reaction is sent to the condenser to cool to 105°C, and then enters the second-stage reactor. The input speed of the second-stage reactor is 2.1 tons / hour, the feed temperat...
Embodiment 3
[0036] like figure 1 As shown, firstly feed phenol and nonene as raw materials into the deferrization column reactor to remove iron ions, then preheat the phenol to 120°C, then fully mix the nonene and the preheated phenol, the mixing ratio It is phenol:nonene=2:1. The mixed materials enter the three-stage fixed-bed adiabatic reaction device in turn, and each stage of the reactor is filled with 5 cubic meters of special resin catalyst for alkylphenol. The catalyst is A36 type special resin catalyst for alkylphenol produced by Rohm and Haas Company . Wherein, the input speed of the first-stage reactor is 1.8 tons / hour, the feed temperature is 120° C., and the opening degree of the bottom valve of the first-stage reactor is controlled to be 30%. The material after the first-stage reaction is sent to the condenser to cool to 100°C, and then enters the second-stage reactor. The input speed of the second-stage reactor is 2 tons / hour, the feed temperature is 100°C, and the feed is...
PUM
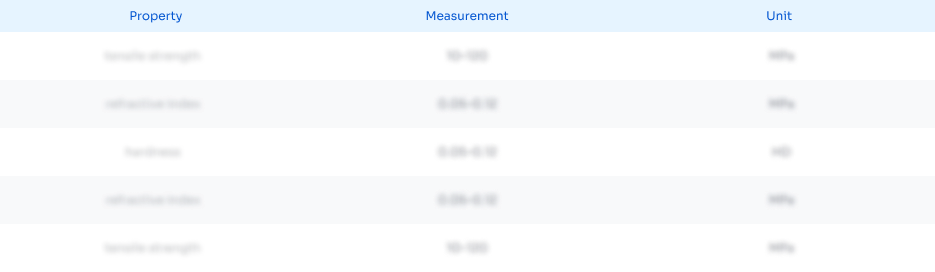
Abstract
Description
Claims
Application Information

- R&D
- Intellectual Property
- Life Sciences
- Materials
- Tech Scout
- Unparalleled Data Quality
- Higher Quality Content
- 60% Fewer Hallucinations
Browse by: Latest US Patents, China's latest patents, Technical Efficacy Thesaurus, Application Domain, Technology Topic, Popular Technical Reports.
© 2025 PatSnap. All rights reserved.Legal|Privacy policy|Modern Slavery Act Transparency Statement|Sitemap|About US| Contact US: help@patsnap.com