High magnetic conductivity and low loss factor manganese-zinc ferrite material and manufacture process thereof
A manganese zinc ferrite, high magnetic permeability technology, applied in the field of manganese zinc ferrite materials, can solve the problems of not meeting the requirements of energy saving and environmental protection, high loss, etc.
- Summary
- Abstract
- Description
- Claims
- Application Information
AI Technical Summary
Problems solved by technology
Method used
Examples
Embodiment 1
[0025] Manganese zinc ferrite material with high magnetic permeability and low loss factor is prepared according to the following method:
[0026] (1) prepare materials according to the following formula:
[0027] Main ingredient: Fe 2 o 3 53mol%, MnO23mol%, ZnO24mol%;
[0028] Auxiliary components (according to the mass percentage of main components): P 2 o 5 0.005wt%, CaO 0.02wt%, SiO 2 0.006wt%, Bi 2 o 3 0.01wt%, MoO 3 0.005wt%, Ta 2 o 5 0.03wt%;
[0029] (2) Mixing: the main components are mixed, and the powder is obtained after mixing for 0.5 hours with a vibrating ball mill;
[0030] (3) Pre-burning: pre-burning the above-mentioned mixed powder at 840°C for 2 hours to obtain a pre-fired material;
[0031] (4) Sand milling: put the above-mentioned calcined material into a sand mill, add auxiliary components, deionized water with a total weight of 50wt% of main components and auxiliary components, and 0.6-1.0wt% of total weight of main components and auxi...
Embodiment 2
[0041] (1) prepare materials according to the following formula:
[0042] Main ingredient: Fe 2 o 3 53mol%, MnO24mol%, ZnO23mol%;
[0043] Auxiliary components (according to the mass percentage of main components): P 2 o 5 0.003wt%, Bi 2 o 3 0.02wt%, MoO 3 0.005wt%, Ta 2 o 5 0.01wt%, ZrO 2 0.03wt%;
[0044] (2) Mixing: the main components are mixed, and the powder is obtained after mixing for 1 hour with a vibrating ball mill;
[0045](3) Calcination: Precalcining the above-mentioned mixed powder at 900°C for 2 hours to obtain a calcining material;
[0046] (4) Sand milling: put the above-mentioned calcined material into a sand mill, add auxiliary components, deionized water with a total weight of 50wt% of main components and auxiliary components, and 0.6-1.0wt% of total weight of main components and auxiliary components. polyvinyl alcohol;
[0047] Sand milling is carried out in stages. The speed of the sand mill at each stage is fast and then slow. The firs...
Embodiment 3
[0056] (1) prepare materials according to the following formula:
[0057] Main ingredient: Fe 2 o 3 54mol%, MnO23mol%, ZnO23mol%;
[0058] Auxiliary components (according to the mass percentage of main components): P 2 o 5 0.003wt%, CaO 0.01wt%, Bi 2 o 3 0.02wt%, MoO 3 0.01wt%, Nb 2 o 5 0.01wt%;
[0059] (2) Mixing: the main components are mixed, and the powder is obtained after mixing for 0.5 hours with a vibrating ball mill;
[0060] (3) Calcination: Precalcining the above-mentioned mixed powder for 2 hours at 880°C to obtain a calcining material;
[0061] (4) Sand milling: put the above-mentioned calcined material into a sand mill, add auxiliary components, deionized water with a total weight of 50wt% of main components and auxiliary components, and 0.6-1.0wt% of total weight of main components and auxiliary components. polyvinyl alcohol;
[0062] Sand milling is carried out in stages. The speed of the sand mill at each stage is first fast and then slow. Th...
PUM
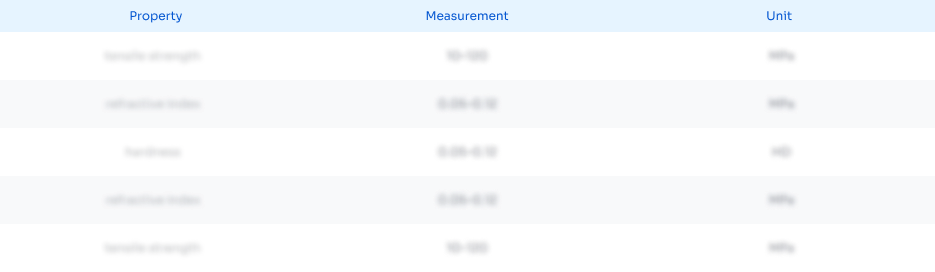
Abstract
Description
Claims
Application Information

- R&D Engineer
- R&D Manager
- IP Professional
- Industry Leading Data Capabilities
- Powerful AI technology
- Patent DNA Extraction
Browse by: Latest US Patents, China's latest patents, Technical Efficacy Thesaurus, Application Domain, Technology Topic, Popular Technical Reports.
© 2024 PatSnap. All rights reserved.Legal|Privacy policy|Modern Slavery Act Transparency Statement|Sitemap|About US| Contact US: help@patsnap.com