On-line detection and compensation system applied to bend processing
A compensation system and pipe bending technology, which is applied in general control systems, control/regulation systems, instruments, etc., can solve the problems of poor reliability and low bending accuracy, and achieve the effect of good reliability and improved bending accuracy
- Summary
- Abstract
- Description
- Claims
- Application Information
AI Technical Summary
Problems solved by technology
Method used
Image
Examples
Embodiment Construction
[0021] The present invention will be further described below in conjunction with the drawings.
[0022] Reference figure 1 , figure 2 , An online detection and compensation system used in pipe bending processing, including a numerical control pipe bending machine used for pipe bending processing, an image acquisition device used for image acquisition, and a numerical control system used for online detection and compensation System, the pipe bending station of the numerical control pipe bending machine is located within the visual range of the image acquisition device, and the numerical control system 1 includes:
[0023] The action execution module is used to control the work of the CNC pipe bending machine. When the bending is performed, the processing bending angle is θ′=(1+K)θ+θ 1 , Where θ is the tube design value, θ 1 Is the theoretical rebound value, K is the compensation parameter; θ 1 The calculation formula is as follows:
[0024] θ 1 = M max ρ ...
PUM
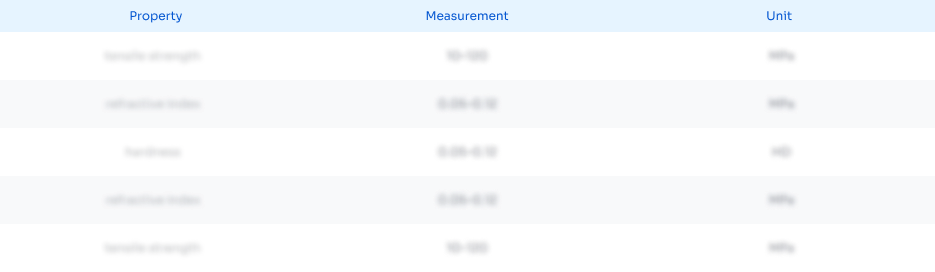
Abstract
Description
Claims
Application Information

- R&D
- Intellectual Property
- Life Sciences
- Materials
- Tech Scout
- Unparalleled Data Quality
- Higher Quality Content
- 60% Fewer Hallucinations
Browse by: Latest US Patents, China's latest patents, Technical Efficacy Thesaurus, Application Domain, Technology Topic, Popular Technical Reports.
© 2025 PatSnap. All rights reserved.Legal|Privacy policy|Modern Slavery Act Transparency Statement|Sitemap|About US| Contact US: help@patsnap.com