capacitive rotation sensor
A rotation sensor, capacitive technology, applied in the direction of conversion sensor output, capacitance measurement, instrument, etc., can solve the problem of rotor disc imbalance or impact, complex structure, complicated and other problems, and achieve the effect of preventing warping or impact
- Summary
- Abstract
- Description
- Claims
- Application Information
AI Technical Summary
Problems solved by technology
Method used
Image
Examples
Embodiment Construction
[0057] Such as figure 1 and 2 As shown, the capacitive rotation sensor proposed by the present invention mainly includes a shell flange 1 made of aluminum casting, which is designed to be cylindrical, and a clamping frame is arranged in its inner hole. Tight ball bearings 2 form the device.
[0058] The ball bearing 2 is preferably designed as a deep groove ball bearing. According to another development, it can be provided that the ball bearing is designed as a sliding bearing or generally as a rolling bearing.
[0059] In the interior, a shaft 3 is supported by a ball bearing 2 , which protrudes with a lower extension from the housing of the capacitive rotary sensor and is secured against falling out by means of a locking ring 4 . This locking ring can also be omitted. However, it can be used to additionally absorb the axial forces transmitted by the shaft 3 to the housing flange 1 .
[0060] In a manner that will be described in more detail below, a rotor support 5, pre...
PUM
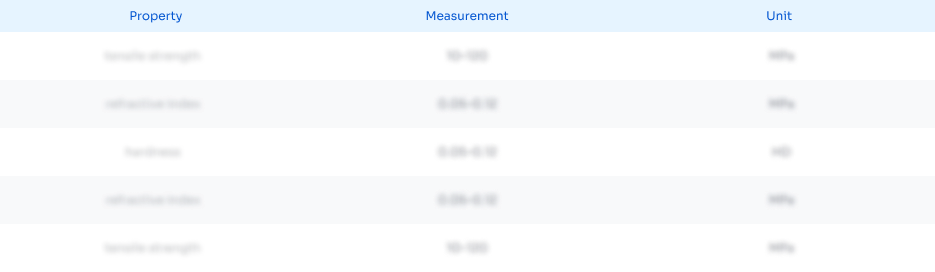
Abstract
Description
Claims
Application Information

- R&D Engineer
- R&D Manager
- IP Professional
- Industry Leading Data Capabilities
- Powerful AI technology
- Patent DNA Extraction
Browse by: Latest US Patents, China's latest patents, Technical Efficacy Thesaurus, Application Domain, Technology Topic, Popular Technical Reports.
© 2024 PatSnap. All rights reserved.Legal|Privacy policy|Modern Slavery Act Transparency Statement|Sitemap|About US| Contact US: help@patsnap.com