Moving die compressive stress decomposing and forming method, volume spring and U-shaped bolt composite bending die
A technology of compressive stress and forming method, applied in the direction of springs, springs/shock absorbers, spring components composed of several springs, etc., can solve the problems of small one-time forming load, large volume, and difficult bending/compounding of forging blanks. , to achieve the effect of low maintenance cost, simple structure and convenient manufacturing
- Summary
- Abstract
- Description
- Claims
- Application Information
AI Technical Summary
Problems solved by technology
Method used
Image
Examples
Embodiment Construction
[0024] From attached figure 1 It can be seen that the mold is mainly composed of an upper mold and a lower mold bounded by U-shaped bolts 3 and a rigid unloader connecting them.
[0025] The material plate is composed of 2, the upper mold is the punch 4 and the punch base 1 is fixedly connected, the lower mold is the movable die 5 with the movable die base 8 as the assembly base, the single-head volume spring 7, the pressure plate 9, and the guide plate 6 composition. attached figure 2 The spring shown is a single-head volume spring 7, the case cover 20 is movably connected with the pressure regulating bolt 18 and the back nut 16, the outer shell 19 and the case cover 20 are fixedly connected with a sealing ring b14, and the rubber 17 is put into the case Insert the sealing ring a12 into the outer wall of the plunger head 15 in the containing cavity of the body 19, insert the air release plug 13 into the pressure insurance block 12 and insert the plunger head 15 into the gu...
PUM
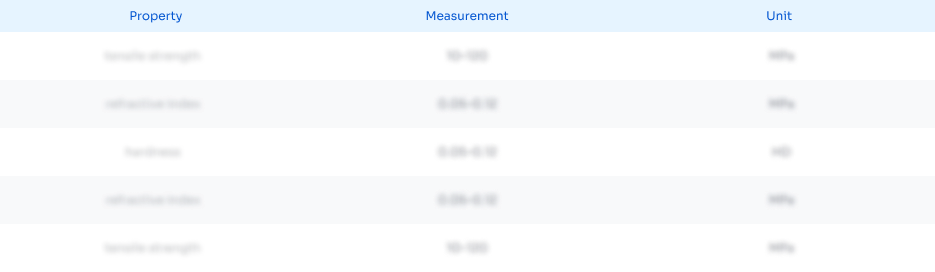
Abstract
Description
Claims
Application Information

- R&D Engineer
- R&D Manager
- IP Professional
- Industry Leading Data Capabilities
- Powerful AI technology
- Patent DNA Extraction
Browse by: Latest US Patents, China's latest patents, Technical Efficacy Thesaurus, Application Domain, Technology Topic, Popular Technical Reports.
© 2024 PatSnap. All rights reserved.Legal|Privacy policy|Modern Slavery Act Transparency Statement|Sitemap|About US| Contact US: help@patsnap.com