Film coating manufacturing process of capacitive touch screen
A technology of capacitive touch screen and production process, applied in metal material coating process, sputtering coating, ion implantation coating and other directions, can solve the problems of blurred image characters, serious reflection of capacitive screen, color distortion, etc.
- Summary
- Abstract
- Description
- Claims
- Application Information
AI Technical Summary
Problems solved by technology
Method used
Examples
Embodiment 1
[0038] Before the coating, the semi-tempered glass substrate is cleaned and dried by heat, and then placed on the shelf for SiO coating 2 +ITO film, the coating adopts Lihe Thin Film Technology vertical automatic continuous magnetron sputtering coating machine, the substrate heating temperature is 280°C, the transmission speed frequency of the coating room is 17.0HZ, and SiO is plated in the No. 4 room 2 , SiO 2 Sputtering power 3500W, O 2 The flow rate is 35Sccm, the Ar flow rate is 200-220Sccm, and the vacuum degree is 3.0×10 -1 Pa~4.5×10 -1 Between Pa, the total air pressure is 0.40-0.45Pa, use 2 SiO2 targets to coat SiO2 film, use 2 ITO targets to coat ITO film, and 8 MoAlMo targets to coat MoAlMo film, the Ar flow rate in the coating chamber is 200-220Sccm, coating Chamber vacuum 4.0*10 -1 Pa~4.5*10 -1 Pa between. Test results: the SiO2 film thickness of the base layer is SiO2 transmittance is 90.5%; ITO film thickness The surface resistance of ITO film is 100Ω / ...
Embodiment 2
[0040] Before the coating, the semi-tempered glass substrate is cleaned on a flat plate, heat-dried and dried, and then placed on the shelf to be coated with SiO2+ITO film. The coating adopts a vertical automatic continuous magnetron sputtering coating machine of Lihe Thin Film Technology, and the substrate is heated. The temperature is 260°C, the transmission speed frequency of the coating chamber is 17.0HZ (the substrate transmission speed of the coating chamber), SiO2 is plated in the No. 4 chamber, the SiO2 sputtering power is 3300W, the O2 flow rate is 35Sccm, the Ar flow rate is 200~220Sccm, and the vacuum degree is 3.0×10 -1 Pa~4.5×10 -1 Between Pa, the total air pressure is 0.40-0.45Pa, use 2 SiO2 targets to coat SiO2 film, use 2 ITO targets to coat ITO film, and 8 MoAlMo targets to coat MoAlMo film, the Ar flow rate in the coating chamber is 200-220Sccm, coating Chamber vacuum 4.0*10 -1 Pa~4.5*10 -1 Pa between. Test results: the SiO2 film thickness of the base laye...
Embodiment 3
[0042] Before the coating, the semi-tempered glass substrate is cleaned on a flat plate, heat-dried and dried, and then placed on the shelf to be coated with SiO2+ITO film. The coating adopts a vertical automatic continuous magnetron sputtering coating machine of Lihe Thin Film Technology, and the substrate is heated. The temperature is 230°C, the transmission speed frequency of the coating chamber is 16.50HZ (the substrate transmission speed of the coating chamber), SiO2 is plated in the No. 4 chamber, the SiO2 sputtering power is 3000W, the O2 flow rate is 35Sccm, the Ar flow rate is 200-220Sccm, and the vacuum degree is 3.0×10 -1 Pa~4.5×10 -1 Between Pa, the total air pressure is 0.40-0.45Pa, use 2 SiO2 targets to coat SiO2 film, use 2 ITO targets to coat ITO film, and 8 MoAlMo targets to coat MoAlMo film, the Ar flow rate in the coating chamber is 200-220Sccm, coating Chamber vacuum 4.0*10 -1 Pa~4.5*10 -1 Pa between. Test results: the SiO2 film thickness of the base lay...
PUM
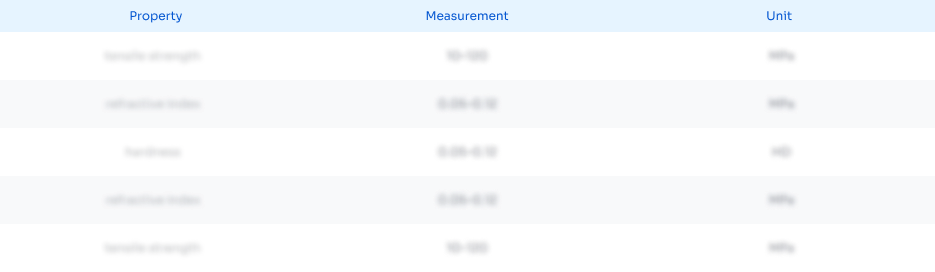
Abstract
Description
Claims
Application Information

- R&D
- Intellectual Property
- Life Sciences
- Materials
- Tech Scout
- Unparalleled Data Quality
- Higher Quality Content
- 60% Fewer Hallucinations
Browse by: Latest US Patents, China's latest patents, Technical Efficacy Thesaurus, Application Domain, Technology Topic, Popular Technical Reports.
© 2025 PatSnap. All rights reserved.Legal|Privacy policy|Modern Slavery Act Transparency Statement|Sitemap|About US| Contact US: help@patsnap.com