Method for preparing high-viscosity sodium carboxymethyl cellulose by utilizing potato starch residues
A technology of sodium carboxymethyl cellulose and potato starch residue, which is applied in fiber raw material processing, textiles and papermaking, etc., can solve problems such as expensive raw materials, and achieve the effects of low production cost, improved product purity, and improved viscosity.
- Summary
- Abstract
- Description
- Claims
- Application Information
AI Technical Summary
Problems solved by technology
Method used
Image
Examples
Embodiment 1
[0027] 1. Preparation of refined cellulose: Add 30 g of potato starch residue and 67.5 g of sulfuric acid with a concentration of 20% in a three-necked bottle, acidify at room temperature for 3 hours, filter and wash with suction; add 90 g of potato starch residue with a concentration of 10 % sodium hydroxide, boiled in alkali at 80°C for 3h, suction filtered and washed; the potato starch slag after alkali cooking was added to 42g in a mass ratio of NaClO:H 2 o 2 = In a 3:4 bleaching solution, stir and bleach at 30°C for 20 minutes; dry at a temperature of 80°C before use.
[0028] 2. Preparation of sodium carboxymethyl cellulose: Add 5 g of refined cellulose and 50 g of ethanol with a concentration of 70% in a three-neck flask, stir and mix evenly, add 3.75 g of sodium hydroxide, and stir at 30°C for 80 minutes to alkalize; then add the concentration 17g of 70% ethanol, 7.0g of chloroacetic acid, after heating up to 70°C for 30min, add 1.25g of sodium hydroxide to the reacti...
Embodiment 2
[0033] 1. Preparation of refined cellulose: Add 30g of potato starch residue and 69g of sulfuric acid with a concentration of 20% in a three-necked bottle, acidify at room temperature for 4 hours, filter and wash with suction; add 100g of potato starch residue with a concentration of 10% after acidification In sodium hydroxide, cook in alkali at 90°C for 3 hours, filter and wash with suction; add the potato starch residue after alkali cooking to 43.5g with a mass ratio of NaClO:H 2 o 2 =3:4 bleaching solution, stirred and bleached at 25°C for 20min; dried at 90°C for later use.
[0034] 2. Preparation of sodium carboxymethyl cellulose: Add 5 g of refined cellulose and 52.5 g of ethanol with a concentration of 70% in a three-neck flask, stir and mix evenly, add 4.125 g of sodium hydroxide, stir and alkalize at 35°C for 60 min; then add Concentration of 70% ethanol 17.5g, chloroacetic acid 7.5g, after heating up to 70°C for 35min, add 1.375g of sodium hydroxide to the reaction ...
Embodiment 3
[0039] 1. Preparation of refined cellulose: Add 30 g of potato starch residue and 70.5 g of sulfuric acid with a concentration of 20% in a three-necked bottle, acidify at room temperature for 3 hours, filter and wash with suction; add 105 g of potato starch residue with a concentration of 10 % sodium hydroxide, boiled in alkali at 90°C for 4h, suction filtered and washed; the potato starch slag after alkali cooking was added to 45g and the mass ratio was NaClO:H 2 o 2 =3:4 bleaching solution, stirred and bleached at 30°C for 20min; dried at 90°C for later use.
[0040] 2. Preparation of sodium carboxymethylcellulose: Add 5g of refined cellulose and 55g of ethanol with a concentration of 70% in a three-neck flask, stir and mix evenly, then add 0.05g of sodium sulfite and 4.5g of sodium hydroxide in sequence, and stir at 35°C for alkalization 60min; then add 18g of ethanol with a concentration of 70% and 8.0g of chloroacetic acid, heat up to 75°C and react for 30min, then add 1...
PUM
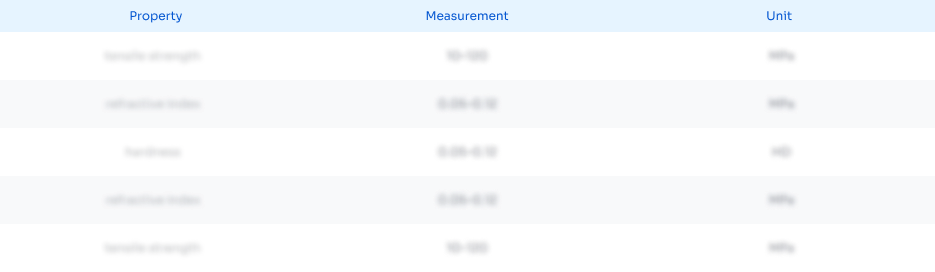
Abstract
Description
Claims
Application Information

- R&D
- Intellectual Property
- Life Sciences
- Materials
- Tech Scout
- Unparalleled Data Quality
- Higher Quality Content
- 60% Fewer Hallucinations
Browse by: Latest US Patents, China's latest patents, Technical Efficacy Thesaurus, Application Domain, Technology Topic, Popular Technical Reports.
© 2025 PatSnap. All rights reserved.Legal|Privacy policy|Modern Slavery Act Transparency Statement|Sitemap|About US| Contact US: help@patsnap.com