Gap sensor calibration system of magnetic-levitation train
A technology of gap sensors and maglev trains, which is applied in the directions of instruments, electromagnetic means, measuring devices, etc., can solve the problems such as the inability to meet the horizontal movement speed requirements of the gap sensors, the inability to calibrate the gap sensors to measure the speed, and the large workload of calibration and maintenance. , to achieve the effect of compact structure, low cost, overcoming wear and tear
- Summary
- Abstract
- Description
- Claims
- Application Information
AI Technical Summary
Problems solved by technology
Method used
Image
Examples
Embodiment Construction
[0017] Such as figure 1 and figure 2 As shown, the maglev train gap sensor calibration system in this embodiment includes a base 1, a sensor fixture 2 for installing the gap sensor 9 to be calibrated, a vertical drive unit 3, a control mechanism and a track 8 located on the base 1, and the sensor The fixture 2 is fixed on the vertical drive unit 3, the track 8 is arranged directly below the sensor fixture 2, the base 1 is provided with a horizontal drive unit 4, the vertical drive unit 3 is fixed on the horizontal drive unit 4 and can be driven by the horizontal drive unit 4 The drive moves along the horizontal direction, and more than one joint 83 is provided on the track 8, and the control mechanism is respectively connected with the vertical drive unit 3, the horizontal drive unit 4 and the gap sensor 9 to be calibrated.
[0018] In this embodiment, the control mechanism includes a control unit 5, a communication unit 6 and a main control unit 7, the control unit 5 is con...
PUM
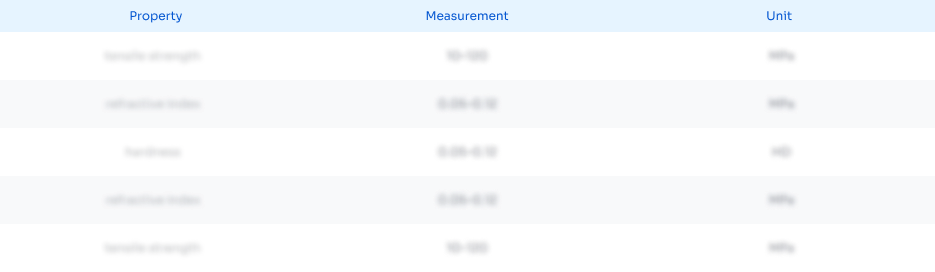
Abstract
Description
Claims
Application Information

- R&D Engineer
- R&D Manager
- IP Professional
- Industry Leading Data Capabilities
- Powerful AI technology
- Patent DNA Extraction
Browse by: Latest US Patents, China's latest patents, Technical Efficacy Thesaurus, Application Domain, Technology Topic, Popular Technical Reports.
© 2024 PatSnap. All rights reserved.Legal|Privacy policy|Modern Slavery Act Transparency Statement|Sitemap|About US| Contact US: help@patsnap.com