Method for preparing modified natural rubber by replacing carbon black with activated pulverized fuel ash
A technology of natural rubber and fly ash, which is applied in the field of rubber composite material preparation to achieve high economic benefits, lower use costs, and simple production methods
- Summary
- Abstract
- Description
- Claims
- Application Information
AI Technical Summary
Problems solved by technology
Method used
Image
Examples
Embodiment 1
[0018] A method for replacing carbon black modified natural rubber with activated fly ash BH-2 modified by a stearic acid coupling agent.
[0019] The method is to add stearic acid, zinc oxide, various accelerators and anti-aging agents in the rubber mixing process on the basis of keeping the modified natural rubber process flow unchanged, and the modified activated pulverized coal Ash BH-2 is directly added to natural rubber and fully mixed with natural rubber to obtain raw rubber, which is vulcanized and molded to make a modified natural rubber in which carbon black is replaced by activated fly ash BH-2;
[0020] Its specific steps include:
[0021] A. Preparation of modified activated fly ash BH-2:
[0022] ①. Vacuum drying: Use the screened fly ash after wet treatment in power plants with an average particle size of 100nm, and dry it in vacuum at 120°C for 12 hours to remove the moisture;
[0023] ②, Activation treatment: Pour the fly ash after vacuum drying into a high-...
Embodiment 2
[0038] A method for replacing carbon black modified natural rubber with BH-3 activated fly ash modified by a silane coupling agent.
[0039] The method is to directly add BH-3 activated fly ash modified by silane coupling agent into natural rubber and fully mix with natural rubber on the basis of keeping the modified natural rubber process flow unchanged to obtain a raw material. Rubber, after vulcanization molding, made of modified natural rubber with BH-3 activated fly ash instead of carbon black;
[0040] Its specific steps include:
[0041] A. Preparation of BH-3 activated fly ash;
[0042] B. Utilize the rubber mixer to masticate the natural rubber at room temperature;
[0043] C. Vulcanization molding;
[0044] Described A, the step of preparing BH-3 activated fly ash comprise:
[0045] ①. Vacuum drying: Utilize the screened and wet-processed fly ash of a power plant with an average particle size of 100nm, and vacuum-dry it at 100°C for 12 hours to remove the moistur...
PUM
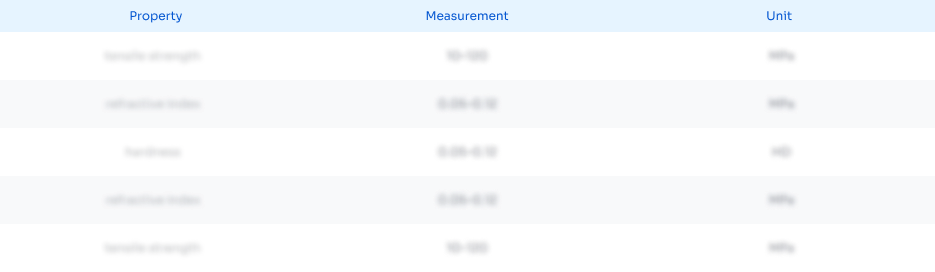
Abstract
Description
Claims
Application Information

- Generate Ideas
- Intellectual Property
- Life Sciences
- Materials
- Tech Scout
- Unparalleled Data Quality
- Higher Quality Content
- 60% Fewer Hallucinations
Browse by: Latest US Patents, China's latest patents, Technical Efficacy Thesaurus, Application Domain, Technology Topic, Popular Technical Reports.
© 2025 PatSnap. All rights reserved.Legal|Privacy policy|Modern Slavery Act Transparency Statement|Sitemap|About US| Contact US: help@patsnap.com