Bearing unit for testing and controlling angular displacement of revolving platform
A technology of angular displacement and rotary table, which is applied in the direction of bearings, bearing components, bearings, etc. in rotating motion, can solve the problems of increased operation error and low rotation angular displacement accuracy, and achieves improved measurement accuracy, improved work accuracy, and convenient installation. Effect
- Summary
- Abstract
- Description
- Claims
- Application Information
AI Technical Summary
Problems solved by technology
Method used
Image
Examples
Embodiment Construction
[0021] Such as figure 1 , figure 2 and image 3 As shown, a bearing unit for angular displacement measurement and control of a rotary table is mainly composed of a worktable 1, a support seat 2, a bearing body 3 between them, a control system 4, a driving device 5 and an angular displacement measuring device 6. The bearing body described above is composed of a moving ring 9 , a stationary ring 10 and a rolling element 11 , and the angular displacement measuring device 6 is composed of a magnetic scale 7 and a sensor 8 .
[0022] Such as figure 1 , figure 2 and image 3 shown, combined with Figure 4 and Figure 5 , a positioning surface I 13 is set on the bottom surface of the workbench 1, the moving coil 9 is fixed with the worktable 1 through the positioning surface I 13, a positioning surface II 14 is set on the top surface of the support seat 2, and the static ring 10 The positioning surface II 14 is fixed together with the supporting seat 2, the rolling body 11 i...
PUM
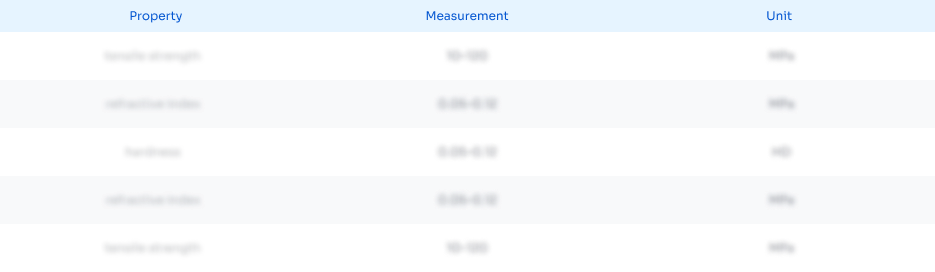
Abstract
Description
Claims
Application Information

- R&D Engineer
- R&D Manager
- IP Professional
- Industry Leading Data Capabilities
- Powerful AI technology
- Patent DNA Extraction
Browse by: Latest US Patents, China's latest patents, Technical Efficacy Thesaurus, Application Domain, Technology Topic, Popular Technical Reports.
© 2024 PatSnap. All rights reserved.Legal|Privacy policy|Modern Slavery Act Transparency Statement|Sitemap|About US| Contact US: help@patsnap.com