Method for implementing feedback moment of friction coupler
A technology of feedback torque and realization method, applied in the direction of clutch, automatic clutch, mechanical equipment, etc., can solve the problems of loss of soft start effect, damage to working machinery, large overload coefficient, etc., to achieve good soft start effect and avoid excessive temperature rise , the effect of large comprehensive overload coefficient
- Summary
- Abstract
- Description
- Claims
- Application Information
AI Technical Summary
Problems solved by technology
Method used
Image
Examples
Embodiment Construction
[0015] Now according to figure 1 The shown feedback control friction coupling principle further illustrates the solution of the present invention.
[0016] Such as figure 1 As shown, the feedback control friction coupler is composed of a driving device and a driven device; the driving device is composed of the driving shaft 1 connected with the driving core 6 installed in the coupler housing 9 through a coupling; the driven device is A device that connects the coupling housing 9 to the drive shaft 1 via bearings 10 .
[0017] During implementation, the core disc circumference part of active movement 6 is processed into left flange 4 and right flange 7 extending to both sides respectively, and the inner surface of flange 4 and 7 is used as driven friction surface; The driven cores 2 and 8 with the same structure as the active core 6 are respectively arranged on the side, and the driven cores 2 and 8 are respectively connected with the coupler housing 9 to rotate together, and...
PUM
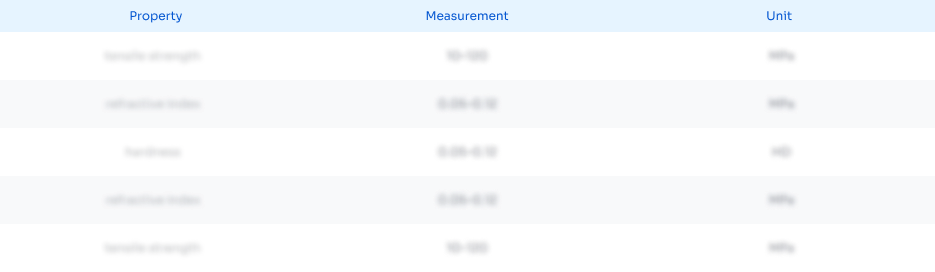
Abstract
Description
Claims
Application Information

- R&D Engineer
- R&D Manager
- IP Professional
- Industry Leading Data Capabilities
- Powerful AI technology
- Patent DNA Extraction
Browse by: Latest US Patents, China's latest patents, Technical Efficacy Thesaurus, Application Domain, Technology Topic, Popular Technical Reports.
© 2024 PatSnap. All rights reserved.Legal|Privacy policy|Modern Slavery Act Transparency Statement|Sitemap|About US| Contact US: help@patsnap.com