Emulsion formed of cashew nut oil and water as plasticizer phenolic molding compound and preparation method thereof
A technology of phenolic molding compound and cashew nut oil, which is applied in the field of phenolic molding compound and its preparation, can solve the problems of poor appearance of injection parts, poor thermal stability of materials, sticking to molds, etc. Effect
- Summary
- Abstract
- Description
- Claims
- Application Information
AI Technical Summary
Problems solved by technology
Method used
Examples
Embodiment 1
[0024] Add 32% of wood powder, 45% of phenolic resin, 7.5% of Hexa, 3% of magnesium oxide, 0.5% of slaked lime, 5% of talcum powder, 3% of calcium carbonate, 2% of calcium stearate, and 2% of oil black into the mixing Mix with normal temperature, add cashew nut oil and an equal amount of water to the mixed material to form an emulsion after vigorously stirring as a plasticizer, then mix for 5 to 20 minutes, use continuous operation roller pressing method, start the plastic refining machine and When it is attached to the equipment, the feeding bag is put down, and the temperature of the front roller is set to 80°C. The temperature of the rear roller is set at 135°C, so that the material slowly falls into the feeding end of the roller. When the roller is covered with a layer of material, the coulter can be put down. Send it to the conveyor belt to let it air-cool, and then break it after cooling.
Embodiment 2
[0026] Put 32% of bamboo powder, 40% of phenolic resin, 7.2% of Hexa, 2% of magnesium oxide, 0.8% of slaked lime, 14% of talcum powder, 2% of calcium stearate, and 2% of oil black into the mixer in turn, and mix with normal temperature Mix evenly under the ground, add cashew nut oil and an equal amount of water to the mixed material to form an emulsion after vigorously stirring as a plasticizer, and then mix for 5 to 20 minutes, use continuous operation roller pressing method, start the plastic refining machine and its auxiliary equipment The feeding bag is put down, and the temperature of the front roll is set to 90°C. The temperature of the rear roller is set at 145°C, so that the material slowly falls into the feeding end of the roller. When the roller is covered with a layer of material, the coulter can be put down. Send it to the conveyor belt to let it air-cool, and then break it after cooling.
Embodiment 3
[0028] Put 20% of wood powder, 35% of phenolic resin, 8% of Hexa, 3% of magnesium oxide, 1% of slaked lime, 14% of talcum powder, 15% of mica powder, 2% of zinc stearate, and 2% of oil black into the mixing Mix with normal temperature, add cashew nut oil and an equal amount of water to the mixed material to form an emulsion after vigorously stirring as a plasticizer, then mix for 5 to 20 minutes, use continuous operation roller pressing method, start the plastic refining machine and When it is attached to the equipment, the feeding bag is put down, and the temperature of the front roller is set to 100°C. The temperature of the rear roller is set at 155°C, so that the material slowly falls into the feeding end of the roller. When the roller is covered with a layer of material, the coulter can be put down. The material is cut by several coulters and directly from the discharge end Send it to the conveyor belt to let it air-cool, and then break it after cooling.
[0029] The flu...
PUM
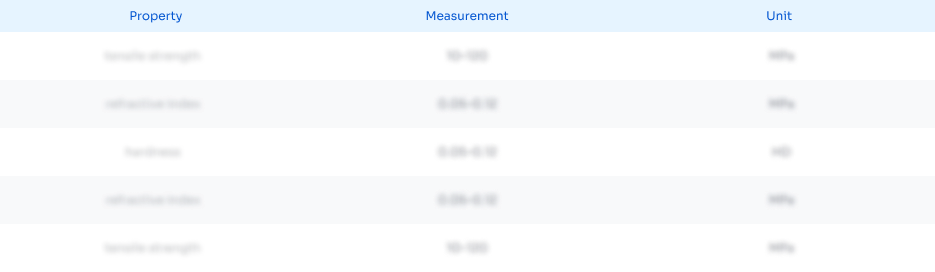
Abstract
Description
Claims
Application Information

- R&D Engineer
- R&D Manager
- IP Professional
- Industry Leading Data Capabilities
- Powerful AI technology
- Patent DNA Extraction
Browse by: Latest US Patents, China's latest patents, Technical Efficacy Thesaurus, Application Domain, Technology Topic, Popular Technical Reports.
© 2024 PatSnap. All rights reserved.Legal|Privacy policy|Modern Slavery Act Transparency Statement|Sitemap|About US| Contact US: help@patsnap.com