Magnetic linkage self-control direct torque control method of brushless DC motor
A direct torque control, brushed DC motor technology, applied in the direction of a single motor speed/torque control, electronic commutator, etc., can solve the problem of complex system control methods, to suppress torque fluctuations, simplify the system, overcome magnetic Estimation of chains and effects of given difficulty
- Summary
- Abstract
- Description
- Claims
- Application Information
AI Technical Summary
Problems solved by technology
Method used
Image
Examples
specific Embodiment approach 1
[0018] Specific implementation mode one: the following combination Figure 1 to Figure 8 Describe this embodiment mode, this embodiment mode first rectifies the power supply AC power source 1 of power frequency through rectifier 2, then obtains DC power source through filter capacitor 3 filtering, then converts described DC power source into AC power source by inverter 4 for the described Brushless DC motor power supply; its control method is:
[0019] Collect the three-phase current value at the input end of the brushless DC motor, and perform three-phase-two-phase coordinate transformation on the three-phase current value, and obtain the component i of the three-phase current value at the input end of the brushless DC motor in the two-phase stationary coordinate system α i β ; Collect the three-phase voltage value of the brushless DC motor input end, and carry out three-phase-two-phase coordinate transformation to the three-phase voltage value, obtain the component of the t...
PUM
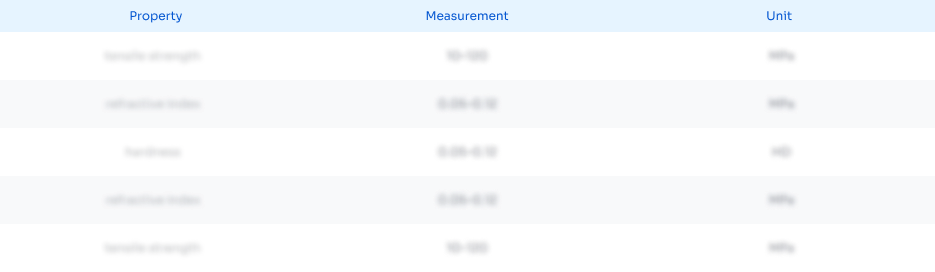
Abstract
Description
Claims
Application Information

- Generate Ideas
- Intellectual Property
- Life Sciences
- Materials
- Tech Scout
- Unparalleled Data Quality
- Higher Quality Content
- 60% Fewer Hallucinations
Browse by: Latest US Patents, China's latest patents, Technical Efficacy Thesaurus, Application Domain, Technology Topic, Popular Technical Reports.
© 2025 PatSnap. All rights reserved.Legal|Privacy policy|Modern Slavery Act Transparency Statement|Sitemap|About US| Contact US: help@patsnap.com