Production method of concrete grouting compound heat-insulating building block
A composite thermal insulation and production method technology, applied in ceramic molding workshops, ceramic molding machines, manufacturing tools, etc., can solve the problems of large energy loss, low production efficiency, and large floor space, so as to avoid manual operation and improve production efficiency Effect
- Summary
- Abstract
- Description
- Claims
- Application Information
AI Technical Summary
Problems solved by technology
Method used
Image
Examples
Embodiment Construction
[0033] Such as figure 1 As shown, the technological process of the production method of the concrete grouting composite thermal insulation block of the present invention includes the following steps: a material preparation department, a forming department, a circuitous transfer and maintenance department, a grouting department and a stacking department. The material preparation department mixes the raw materials of the blocks evenly and then transports them to the forming department. The forming department shapes the hollow blocks through the block forming machine and installs them on the pallet, and then enters the circuitous transfer and maintenance department. Carry out maintenance. During the transfer process, the grouting department grouts the hollow blocks to make them thermal insulation blocks. The cured thermal insulation blocks are stacked by the palletizing department.
[0034] In the material preparation department, the loader sends the aggregate from the aggregate ...
PUM
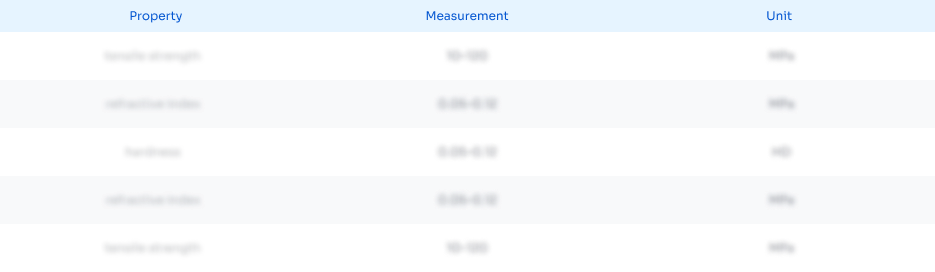
Abstract
Description
Claims
Application Information

- R&D
- Intellectual Property
- Life Sciences
- Materials
- Tech Scout
- Unparalleled Data Quality
- Higher Quality Content
- 60% Fewer Hallucinations
Browse by: Latest US Patents, China's latest patents, Technical Efficacy Thesaurus, Application Domain, Technology Topic, Popular Technical Reports.
© 2025 PatSnap. All rights reserved.Legal|Privacy policy|Modern Slavery Act Transparency Statement|Sitemap|About US| Contact US: help@patsnap.com