Search and rescue robot used in pit
A robotic and mechanical technology, applied in the field of robotics, can solve problems such as unsuitable and non-explosion-proof protection design, and achieve the effects of reducing weight, avoiding cable constraints, and good airtightness
- Summary
- Abstract
- Description
- Claims
- Application Information
AI Technical Summary
Problems solved by technology
Method used
Image
Examples
Embodiment
[0051] Example: such as figure 1 , figure 2 As shown, it includes an explosion-proof casing 1, two sets of symmetrical walking systems 6, independent swing arm systems 5 and control systems 7, and the driving mechanisms of the control system 7, walking system 6 and swing arm systems 5 are placed in the explosion-proof casing 1, The control system 7 is connected to the drive mechanism, and a mechanical pan-tilt 3 and an optical fiber application device 4 are also arranged above the explosion-proof enclosure 1. The mechanical pan-tilt 3 is electrically connected to the control system 7, and the optical fiber application device 4 is connected to the control system 7 through an optical fiber. . .
[0052] Such as image 3 , Figure 4 As shown, the explosion-proof enclosure 1 includes a mobile platform 101 and a positive-pressure upper cover 102 connected with it by screws. Both the mobile platform 101 and the upper cover 102 are frames welded by angle steel, which play a main...
PUM
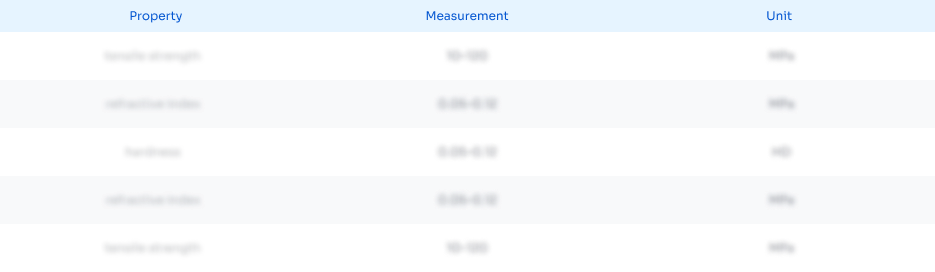
Abstract
Description
Claims
Application Information

- Generate Ideas
- Intellectual Property
- Life Sciences
- Materials
- Tech Scout
- Unparalleled Data Quality
- Higher Quality Content
- 60% Fewer Hallucinations
Browse by: Latest US Patents, China's latest patents, Technical Efficacy Thesaurus, Application Domain, Technology Topic, Popular Technical Reports.
© 2025 PatSnap. All rights reserved.Legal|Privacy policy|Modern Slavery Act Transparency Statement|Sitemap|About US| Contact US: help@patsnap.com