High-frequency decoupling piston magneto-rheological damper
A magneto-rheological damper and piston-type technology, applied in the field of dampers, can solve problems such as poor vibration isolation performance and large dynamic stiffness, achieve the effect of reducing high-frequency dynamic stiffness and damping, and improving high-frequency vibration isolation effect
- Summary
- Abstract
- Description
- Claims
- Application Information
AI Technical Summary
Problems solved by technology
Method used
Image
Examples
specific Embodiment approach 1
[0008] Specific implementation mode one: combine Figure 1 to Figure 3 Describe this specific embodiment, the high-frequency decoupling piston type magnetorheological damper of this embodiment, which includes a cylinder 1, a first end cover 2, a piston 3, a piston rod 4, a coil 5 and a magnetorheological fluid 7 , it also includes a decoupling mechanism 6, the decoupling mechanism 6 includes a first limit baffle 61, a second limit baffle 62, a first compression spring 63 and a second compression spring 64; the piston rod 4 is cylinder, the central axis of the piston 3 has a cylindrical hole, and both ends of the piston 3 are provided with an annular groove with the central axis of the piston 3 as the central axis, and the two annular grooves of the piston 3 are respectively equipped with The first compression spring 63 and the second compression spring 64, and the diameter of the piston rod 4 is less than or equal to the inner diameter of the first compression spring 63 and th...
specific Embodiment approach 2
[0017] Embodiment 2: Different from Embodiment 1, this embodiment also includes a second end cap 8, which has a cylindrical hole, and the piston rod 4 passes through the second end cap from the cylinder 1. The cylindrical hole on the end cover 8 allows the other end of the piston rod 4 to be placed outside the cylinder barrel 1, and the piston rod 4 is in sealing and sliding contact with the second end cover 8 .
specific Embodiment approach 3
[0018] Embodiment 3: The difference from Embodiment 1 or Embodiment 2 is that the second limiting baffle 62 is fixed to the piston rod 4 through fastening screws.
[0019] In this embodiment, the second limit baffle 62 is detachable, which facilitates the assembly and replacement of the piston 3 and the piston rod 4 .
PUM
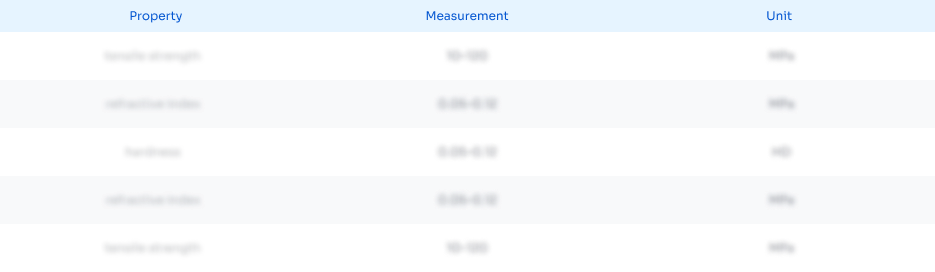
Abstract
Description
Claims
Application Information

- R&D
- Intellectual Property
- Life Sciences
- Materials
- Tech Scout
- Unparalleled Data Quality
- Higher Quality Content
- 60% Fewer Hallucinations
Browse by: Latest US Patents, China's latest patents, Technical Efficacy Thesaurus, Application Domain, Technology Topic, Popular Technical Reports.
© 2025 PatSnap. All rights reserved.Legal|Privacy policy|Modern Slavery Act Transparency Statement|Sitemap|About US| Contact US: help@patsnap.com