Coupling under-actuated integrated three-joint robot finger device
A robot finger and three-joint technology, applied in the direction of manipulators, chucks, manufacturing tools, etc., can solve the problems of inability to realize natural bending of joints, inability to make a fist with empty hands, and inability to realize terminal pinching, etc., to achieve simple and reliable structure, Low cost, great effect
- Summary
- Abstract
- Description
- Claims
- Application Information
AI Technical Summary
Problems solved by technology
Method used
Image
Examples
Embodiment Construction
[0055] The content of the specific structure and working principle of the present invention will be further described in detail below in conjunction with the accompanying drawings and embodiments. The embodiment of the coupled underactuated integrated three-joint robot finger device provided by the present invention is as follows: figure 1 , figure 2 , image 3 , Figure 4 , Figure 5 , Figure 6 , Figure 7 , Figure 8 and Figure 9 As shown, the three-joint robotic finger device includes a base 1, a first finger section 2, a second finger section 3, an end finger section 4, a proximal joint axis 5, a first middle joint axis 6, a second middle joint axis 7, Far joint shaft 8, speed reducer 9 and motor 10; Said motor 10 is fixedly connected with base 1, and the output shaft of motor 10 is connected with the input shaft of said speed reducer 9, and the output shaft of speed reducer 9 is connected with said speed reducer 9. The proximal joint shaft 5 is connected, the p...
PUM
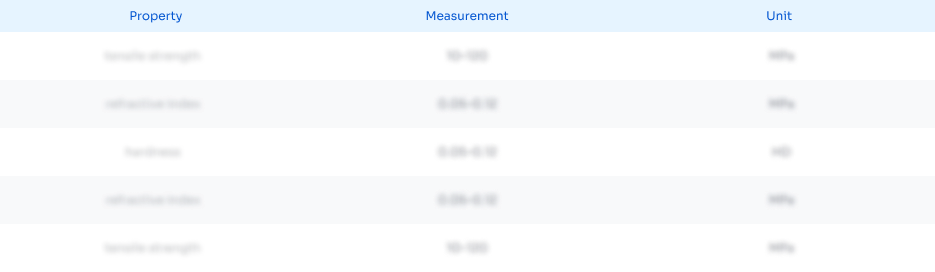
Abstract
Description
Claims
Application Information

- R&D
- Intellectual Property
- Life Sciences
- Materials
- Tech Scout
- Unparalleled Data Quality
- Higher Quality Content
- 60% Fewer Hallucinations
Browse by: Latest US Patents, China's latest patents, Technical Efficacy Thesaurus, Application Domain, Technology Topic, Popular Technical Reports.
© 2025 PatSnap. All rights reserved.Legal|Privacy policy|Modern Slavery Act Transparency Statement|Sitemap|About US| Contact US: help@patsnap.com