Method for preparing fluoroethylene carbonate
A technology of fluoroethylene carbonate and chloroethylene carbonate, which is applied in the direction of organic chemistry, can solve the problems of short reaction time, long time, high reaction temperature, etc., and achieve the effect of easier control of reaction, mild reaction and small dosage
- Summary
- Abstract
- Description
- Claims
- Application Information
AI Technical Summary
Problems solved by technology
Method used
Examples
Embodiment 1
[0019] Mix 50g of sodium fluoride, 130g of chloroethylene carbonate, and 5ml of ionic liquid into a three-necked flask equipped with a condenser, stirrer and thermometer. The reaction temperature is controlled at about 50°C. When the temperature rises to 100°C Insulate for 1 hour, then filter, and the obtained filtrate has a fluoroethylene carbonate content of 92.3%.
Embodiment 2
[0021] Mix 50g of sodium fluoride, 130g of chloroethylene carbonate, and 3ml of ionic liquid into a three-necked flask equipped with a condenser, stirrer and thermometer. The reaction temperature is controlled at about 50°C. When the temperature rises to 100°C Insulate for 1 hour, then filter, and the obtained filtrate has a fluoroethylene carbonate content of 91.6%.
Embodiment 3
[0023] Mix 50g of sodium fluoride, 130g of chloroethylene carbonate, and 1ml of ionic liquid into a three-necked flask equipped with a condenser, stirrer and thermometer. The reaction temperature is controlled at about 50°C. When the temperature rises to 100°C Insulate for 1 hour, then filter, and the obtained filtrate has a fluoroethylene carbonate content of 91.0%.
PUM
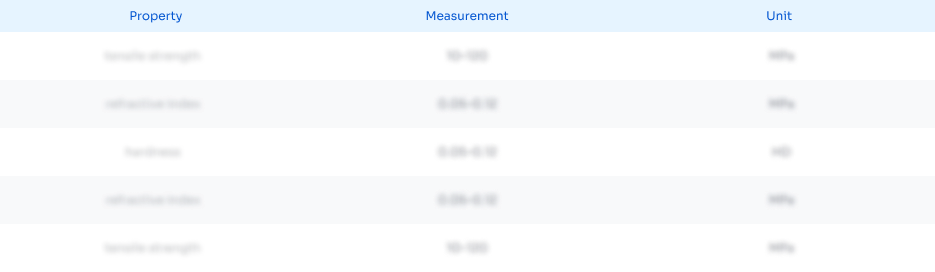
Abstract
Description
Claims
Application Information

- Generate Ideas
- Intellectual Property
- Life Sciences
- Materials
- Tech Scout
- Unparalleled Data Quality
- Higher Quality Content
- 60% Fewer Hallucinations
Browse by: Latest US Patents, China's latest patents, Technical Efficacy Thesaurus, Application Domain, Technology Topic, Popular Technical Reports.
© 2025 PatSnap. All rights reserved.Legal|Privacy policy|Modern Slavery Act Transparency Statement|Sitemap|About US| Contact US: help@patsnap.com