Method for continuously and dynamically removing iron from minerals
A mineral and dynamic technology, applied in chemical instruments and methods, magnetic separation, solid separation, etc., can solve the problems of difficulty in giving magnetic field strength parameters, low efficiency (need to stop to pick up iron, high labor intensity, etc., to achieve low cost Effect
- Summary
- Abstract
- Description
- Claims
- Application Information
AI Technical Summary
Problems solved by technology
Method used
Image
Examples
Embodiment Construction
[0011] see figure 1 , the auxiliary conveyor belt 2 is placed under the unloading end of the main conveyor belt 1 to accept the ore unloaded by the main conveyor belt 1. The auxiliary conveyor belt 2 is functionally divided into two sections, namely the vibration paving section 3 and the magnet adsorption section 5. First, vibrate the piled ore on the auxiliary conveyor belt 2 through the exciter 4. The length of the vibrating paving section depends on the amount of ore conveyed and the excitation parameters of the exciter 4. The parameter selection range is; followed by the magnet The magnetic field strength of the adsorption section 5 and the magnet group 6 depends on the magnetic properties of ferromagnetic minerals and other factors. The amplitude is 1mm-10mm, and the frequency is 5Hz-50Hz; Blocks (or grains) on it can directly contact with the belt surface of the auxiliary conveyor belt 2. The magnets installed on the auxiliary conveyor belt are permanent magnets or elec...
PUM
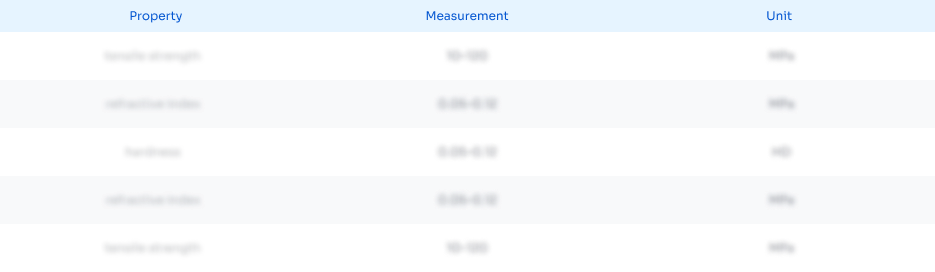
Abstract
Description
Claims
Application Information

- R&D Engineer
- R&D Manager
- IP Professional
- Industry Leading Data Capabilities
- Powerful AI technology
- Patent DNA Extraction
Browse by: Latest US Patents, China's latest patents, Technical Efficacy Thesaurus, Application Domain, Technology Topic, Popular Technical Reports.
© 2024 PatSnap. All rights reserved.Legal|Privacy policy|Modern Slavery Act Transparency Statement|Sitemap|About US| Contact US: help@patsnap.com