Cold-drawing molding process of spline cross shaft
A molding process and cross-axis technology, applied in the field of auto parts manufacturing, to achieve good economic and social benefits, improve productivity and yield, and reduce cutting effects
- Summary
- Abstract
- Description
- Claims
- Application Information
AI Technical Summary
Problems solved by technology
Method used
Examples
Embodiment 1
[0016] The concrete steps of this embodiment are as follows:
[0017] 1. Remove the rust and dirt on the surface of the bar for processing the cross shaft;
[0018] 2. Heat the bar to 850°C;
[0019] 3. Send it into four cold drawing machines with two sets of molds in turn, and carry out cold drawing processing through the molds, and perform eight deformations before forming; among them, the first cold drawing temperature is 850 ° C; the second cold drawing The drawing temperature is 450°C; the third cold drawing temperature is 300°C; the fourth cold drawing temperature is 200°C; the fifth cold drawing temperature is 100°C; the sixth cold drawing temperature is 90°C; The drawing temperature is 70°C; the eighth cold drawing temperature is 50°C;
[0020] 4. Heating the formed cross shaft to 180°C, and then cleaning it to get the finished product.
Embodiment 2
[0022] The concrete steps of this embodiment are as follows:
[0023] 1. Remove the rust and dirt on the surface of the bar for processing the cross shaft;
[0024] 2. Heat the bar to 920°C;
[0025] 3. Send it to four cold drawing machines with two sets of moulds, and carry out cold drawing processing through the moulds, and perform eight deformations before forming; among them, the first cold drawing temperature is 920 ° C; the second cold drawing The drawing temperature is 500°C; the third cold drawing temperature is 350°C; the fourth cold drawing temperature is 260°C; the fifth cold drawing temperature is 150°C; the sixth cold drawing temperature is 100°C; The drawing temperature is 80°C; the eighth cold drawing temperature is 60°C;
[0026] 4. Heating the molded cross shaft to 220°C, and then cleaning it to get the finished product.
Embodiment 3
[0028] The concrete steps of this embodiment are as follows:
[0029] 1. Remove the rust and dirt on the surface of the bar for processing the cross shaft;
[0030] 2. Heat the bar to 900°C;
[0031] 3. Send it to four cold drawing machines with two sets of molds in turn, and carry out cold drawing processing through the molds, and perform eight deformations before forming; among them, the first cold drawing temperature is 900 ° C; the second cold drawing The drawing temperature is 480°C; the third cold drawing temperature is 330°C; the fourth cold drawing temperature is 230°C; the fifth cold drawing temperature is 120°C; the sixth cold drawing temperature is 95°C; The drawing temperature is 75°C; the eighth cold drawing temperature is 55°C;
[0032] 4. Heating the formed cross shaft to 200°C, and then cleaning it to get the finished product.
[0033] In the above-mentioned embodiments, the cross shafts are processed by the process of the present invention, which can be pro...
PUM
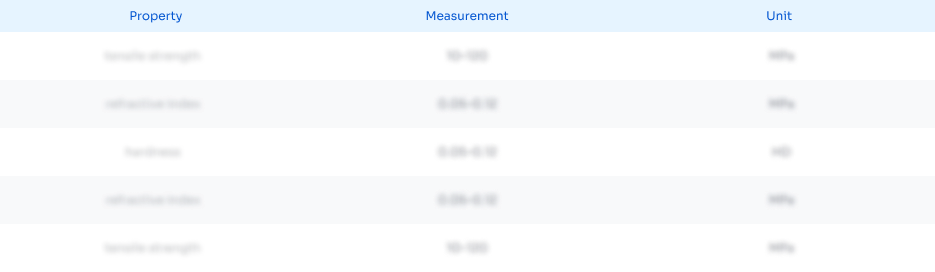
Abstract
Description
Claims
Application Information

- R&D Engineer
- R&D Manager
- IP Professional
- Industry Leading Data Capabilities
- Powerful AI technology
- Patent DNA Extraction
Browse by: Latest US Patents, China's latest patents, Technical Efficacy Thesaurus, Application Domain, Technology Topic, Popular Technical Reports.
© 2024 PatSnap. All rights reserved.Legal|Privacy policy|Modern Slavery Act Transparency Statement|Sitemap|About US| Contact US: help@patsnap.com