Tilting-pad bearing built-in motor
A built-in, bearing technology used in electrical components, electromechanical devices, electrical components, etc.
- Summary
- Abstract
- Description
- Claims
- Application Information
AI Technical Summary
Problems solved by technology
Method used
Image
Examples
Embodiment Construction
[0026] Such as figure 1As shown, the built-in tilting pad bearing motor of the present invention includes a motor main shaft 2, a front end cover assembly 3, a rear end cover assembly 4, a motor stator 5, a motor rotor 6 and a cuboid motor casing 1, and the motor rotor 6 are set on the motor shaft 2, the motor stator 5 is set in the motor box 1, the motor shaft 2 is placed in the motor stator 5, the two ends of the motor stator 5 are provided with a sealing plate 7, and the sealing plate 7 is set in the Outside the motor shaft 2, it is fixedly connected with the motor case 1 and the motor stator 5. The front end cover assembly 3 includes a front flange 31 and a front tilting pad bearing 32 supported between the front flange 31 and the motor shaft 2. The flange 31 is fixed on the front end of the motor case 1, the rear end cover assembly 4 includes a rear flange 41 and a rear tilting pad bearing 42 supported between the rear flange 41 and the motor main shaft 2, and the rear f...
PUM
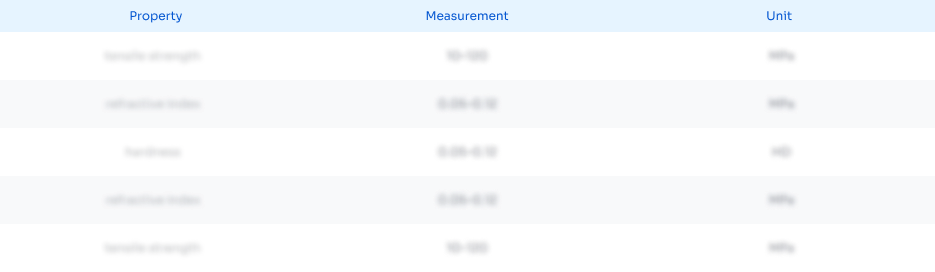
Abstract
Description
Claims
Application Information

- R&D
- Intellectual Property
- Life Sciences
- Materials
- Tech Scout
- Unparalleled Data Quality
- Higher Quality Content
- 60% Fewer Hallucinations
Browse by: Latest US Patents, China's latest patents, Technical Efficacy Thesaurus, Application Domain, Technology Topic, Popular Technical Reports.
© 2025 PatSnap. All rights reserved.Legal|Privacy policy|Modern Slavery Act Transparency Statement|Sitemap|About US| Contact US: help@patsnap.com