Method for producing printed board combining rigidness and flexibleness
A production method and a combination of rigid and flexible technology, which is applied in the fields of printed circuit manufacturing, printed circuit, printed circuit assembly of electrical components, etc., can solve the problems of difficult lamination of covering film, expensive PTFE material, difficult selection, etc., and achieves a solution The difficulty of choosing gaskets, avoiding production quality problems, and improving the effect of production quality
- Summary
- Abstract
- Description
- Claims
- Application Information
AI Technical Summary
Problems solved by technology
Method used
Image
Examples
Embodiment Construction
[0026] The purpose of the present invention is to provide a method for opening windows of rigid-flexible printed boards, using existing equipment, and by improving the production process, it overcomes the difficulties in the previous production process and more effectively produces products that meet the quality requirements. Rigid-flex printed boards.
[0027] Before laminating the rigid part and the flexible part of the rigid-flex printed circuit, the preprocessing of the rigid part and the flexible part is carried out separately.
[0028] refer to figure 2 , figure 2 It is a flow chart of the production method of a rigid-flexible printed board of the present invention; first, according to the circuit production process of the prior art, S1: open the flexible board, rigid board, cover film, and low resin fluidity prepreg; S21 : Then transfer the inner layer circuit pattern to each layer of the flexible board, S22: Etch the circuit on the flexible board; S31: Then open th...
PUM
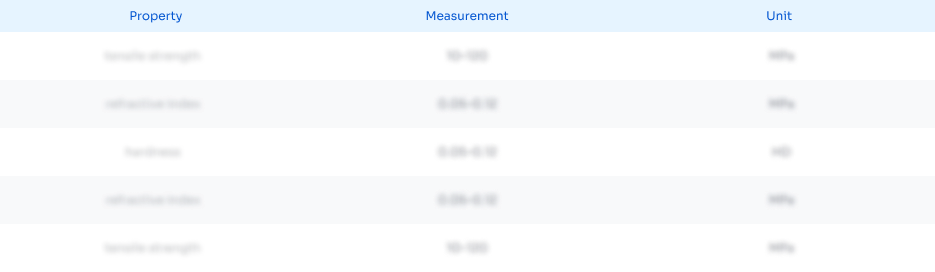
Abstract
Description
Claims
Application Information

- R&D
- Intellectual Property
- Life Sciences
- Materials
- Tech Scout
- Unparalleled Data Quality
- Higher Quality Content
- 60% Fewer Hallucinations
Browse by: Latest US Patents, China's latest patents, Technical Efficacy Thesaurus, Application Domain, Technology Topic, Popular Technical Reports.
© 2025 PatSnap. All rights reserved.Legal|Privacy policy|Modern Slavery Act Transparency Statement|Sitemap|About US| Contact US: help@patsnap.com