Energy-saving using method for circular batching of carbon mother liquor
A technology of carbon separation and evaporation of mother liquor, which is applied in the direction of carbonate preparation, bicarbonate preparation, alkali metal aluminate/alumina/aluminum hydroxide preparation, etc. Alkali boiling, frequent washing, frequent parking and other problems, to achieve the effect of promoting and applying in industrialization, significant economic and social benefits, and good energy saving effect
- Summary
- Abstract
- Description
- Claims
- Application Information
AI Technical Summary
Problems solved by technology
Method used
Examples
Embodiment 1
[0018] The energy-saving carbon-separated mother liquor circulating batching using method of the present invention is carried out according to the following steps successively:
[0019] (1) The temperature is 70-80°C, Na 2 CO 3 Concentration of 345g / l, Al 2 o 3 The high-concentration carbon fraction mother liquor with a concentration of 0.6g / l is pumped into the carbonization tower, and flows down from the top of the tower through each layer of sieve plates, with a pressure ≥ 2.5kgf / m 2 CO 2 The gas goes up through the pipeline from the bottom of the carbonization tower through the ventilation holes of each layer of sieve plates, and contacts with the high-concentration carbon mother liquor in reverse to react to form sodium bicarbonate and form sodium bicarbonate slurry.
[0020] (2) The sodium bicarbonate slurry at 60-65°C is pumped to a vacuum drum filter or a horizontal belt filter for liquid-solid separation. The separated sodium bicarbonate crystals are recycled for...
Embodiment 2
[0024] The energy-saving carbon-separated mother liquor circulating batching using method of the present invention is carried out according to the following steps successively:
[0025] (1) The temperature is 70-80°C, Na 2 CO 3 Concentration of 355g / l, Al 2 o 3 The high-concentration carbon fraction mother liquor with a concentration of 0.9g / l is pumped into the carbonization tower, and flows down from the top of the tower through each layer of sieve plates, with a pressure ≥ 2.5kgf / m 2 CO 2 The gas goes up through the pipeline from the bottom of the carbonization tower through the ventilation holes of each layer of sieve plates, and contacts with the high-concentration carbon mother liquor in reverse to react to form sodium bicarbonate and form sodium bicarbonate slurry.
[0026] (2) The sodium bicarbonate slurry at 60-65°C is pumped to a vacuum drum filter or a horizontal belt filter for liquid-solid separation. The separated sodium bicarbonate crystals are recycled for...
Embodiment 3
[0030] The energy-saving carbon-separated mother liquor circulating batching using method of the present invention is carried out according to the following steps successively:
[0031] (1) The temperature is 70-80°C, Na 2 CO 3 Concentration of 345g / l, Al 2 o 3 The high-concentration carbon mother liquor with a concentration of 0.8g / l is pumped into the carbonization tower, and flows downward from the top of the tower through various sieve plates, with a pressure ≥ 2.5kgf / m 2 CO 2 The gas goes up through the pipeline from the bottom of the carbonization tower through the ventilation holes of each layer of sieve plates, and contacts with the high-concentration carbon mother liquor in reverse to react to form sodium bicarbonate and form sodium bicarbonate slurry.
[0032] (2) The sodium bicarbonate slurry at 60-65°C is pumped to a vacuum drum filter or a horizontal belt filter for liquid-solid separation. The separated sodium bicarbonate crystals are recycled for batching, ...
PUM
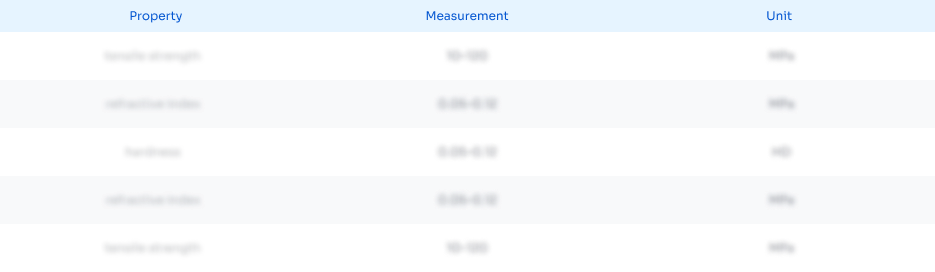
Abstract
Description
Claims
Application Information

- R&D
- Intellectual Property
- Life Sciences
- Materials
- Tech Scout
- Unparalleled Data Quality
- Higher Quality Content
- 60% Fewer Hallucinations
Browse by: Latest US Patents, China's latest patents, Technical Efficacy Thesaurus, Application Domain, Technology Topic, Popular Technical Reports.
© 2025 PatSnap. All rights reserved.Legal|Privacy policy|Modern Slavery Act Transparency Statement|Sitemap|About US| Contact US: help@patsnap.com