Hot melting connecting method of plastic composite pipe and connecting device used by same
A connection method and a connection device technology, which are applied in the direction of pipeline connection arrangement, pipe/pipe joint/pipe fitting, mechanical equipment, etc., can solve the problems of unfavorable product competition, many processing procedures, complex processes, etc., and achieve easy processing and low connection cost , the effect of reliable connection
- Summary
- Abstract
- Description
- Claims
- Application Information
AI Technical Summary
Problems solved by technology
Method used
Image
Examples
Embodiment
[0017] Example: figure 1 Schematically illustrates the structural type of the hot-melt socket connection of the steel wire skeleton plastic composite pipe, two sections of the steel wire skeleton plastic composite pipe are connected as a whole through the splicing bonding surface. When connecting, the outer surface of the unflared end 8 and the inner surface of the flared end 1 at the connection end of the above-mentioned two sections of steel wire skeleton plastic composite pipe are respectively heated to a molten state with molds 5 and 3, and then the heating device is removed, and the two The heated surfaces of the pipe sections are plugged together, and after cooling, the connection of the two steel wire frame plastic composite pipes is completed.
[0018] The flaring and shaping method of the steel mesh skeleton plastic composite pipe is: firstly heat the nozzle of the pipe to the softening temperature, pass through the flaring mold and hydraulic press, mold and shape, an...
PUM
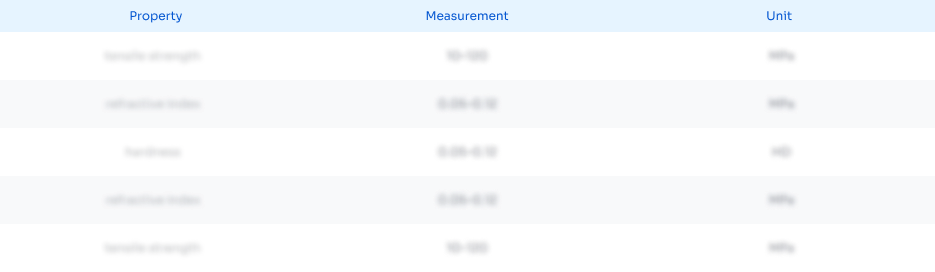
Abstract
Description
Claims
Application Information

- R&D
- Intellectual Property
- Life Sciences
- Materials
- Tech Scout
- Unparalleled Data Quality
- Higher Quality Content
- 60% Fewer Hallucinations
Browse by: Latest US Patents, China's latest patents, Technical Efficacy Thesaurus, Application Domain, Technology Topic, Popular Technical Reports.
© 2025 PatSnap. All rights reserved.Legal|Privacy policy|Modern Slavery Act Transparency Statement|Sitemap|About US| Contact US: help@patsnap.com