Rockwell sealing ring and production method thereof
A kind of sealing ring, Rock style technology, applied in the direction of engine sealing, mechanical equipment, engine components, etc., can solve the problems of small installation position of skeleton sealing ring, poor overall rigidity, high working strength, etc., to achieve convenient installation and disassembly, reduce Processing cost and the effect of improving processing efficiency
- Summary
- Abstract
- Description
- Claims
- Application Information
AI Technical Summary
Problems solved by technology
Method used
Image
Examples
Embodiment 1
[0042] Such as figure 1 , figure 2 with image 3 The Rocky sealing ring shown includes a main sealing ring 1 and a secondary sealing ring 2 parallel to each other. The other end surface of the main sealing ring 1 is provided with an annular protrusion 3, and the end surface of one side of the secondary sealing ring 2 is provided with an annular recess. Groove 4, annular protrusion 3 embedded in the annular groove 4; the outer peripheral surface of the main sealing ring 1 is provided with a groove 5, and the elastic ring 6 is embedded in the groove 5, and the inner peripheral surface of the main sealing ring 1 is provided with a sealing main lip 7.
[0043] According to actual working conditions, the outer peripheral surface of the auxiliary sealing ring 2 is provided with two protrusions 8 .
[0044] In order to strengthen the sealing effect of the main sealing lip 7 , one end surface of the main sealing ring 1 is provided with an annular groove 9 , and a spring ring 10 i...
Embodiment 2
[0064] This embodiment is identical with embodiment 1 except following feature:
[0065] The other end surface of the main sealing ring is provided with an annular protrusion and an annular groove, and one end surface of the auxiliary sealing ring is provided with an annular groove and an annular protrusion, and the main sealing ring and the auxiliary sealing ring are embedded and connected with each other.
PUM
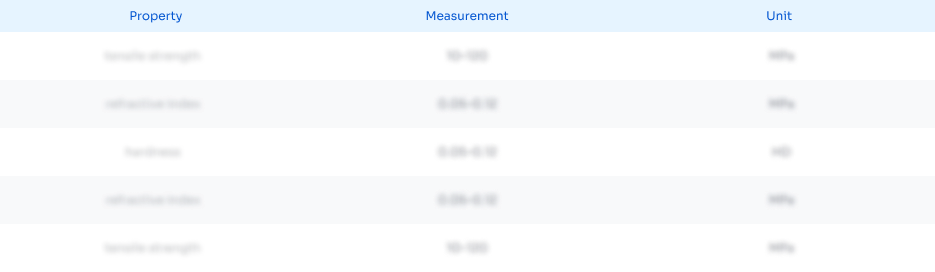
Abstract
Description
Claims
Application Information

- R&D
- Intellectual Property
- Life Sciences
- Materials
- Tech Scout
- Unparalleled Data Quality
- Higher Quality Content
- 60% Fewer Hallucinations
Browse by: Latest US Patents, China's latest patents, Technical Efficacy Thesaurus, Application Domain, Technology Topic, Popular Technical Reports.
© 2025 PatSnap. All rights reserved.Legal|Privacy policy|Modern Slavery Act Transparency Statement|Sitemap|About US| Contact US: help@patsnap.com