Two-section type molding method of metal plate
A forming method and metal plate technology, applied in the field of metal plate forming, can solve the problems of long manufacturing time, unfavorable mass production, and slow forming speed, so as to reduce elastic recovery and stress residue, improve production rate and efficiency, and improve the outer surface good texture effect
- Summary
- Abstract
- Description
- Claims
- Application Information
AI Technical Summary
Problems solved by technology
Method used
Image
Examples
Embodiment Construction
[0031] The detailed description and technical content of the present invention are described below with the accompanying drawings, but the attached drawings are only provided for reference and description, and are not intended to limit the present invention.
[0032] Please refer to Figure 1 to Figure 5 Shown are respectively the production flow chart of the two-stage forming method of the metal plate of the present invention, the cross-sectional view of the metal plate inserted into the forming device in the method, the plastic forming in the first stage of the method, and the A cross-sectional view of the high-pressure gas injection molding apparatus and a cross-sectional view of the plastic forming in the second stage of the method. The invention provides a two-stage forming method of a metal plate, the method steps comprising:
[0033] Step a: molding device 10 is provided, and this molding device 10 comprises mold base 11 and sealing mold 12, and this sealing mold 12 is...
PUM
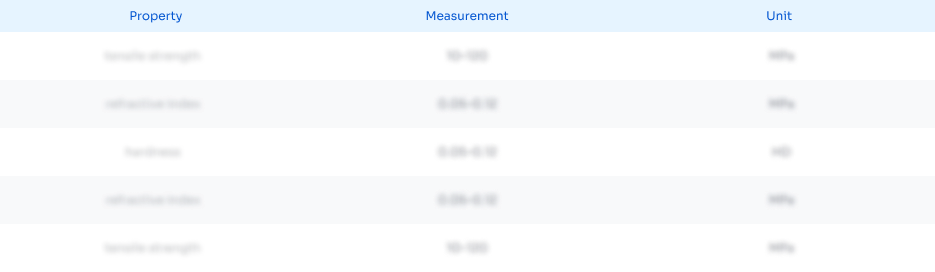
Abstract
Description
Claims
Application Information

- R&D
- Intellectual Property
- Life Sciences
- Materials
- Tech Scout
- Unparalleled Data Quality
- Higher Quality Content
- 60% Fewer Hallucinations
Browse by: Latest US Patents, China's latest patents, Technical Efficacy Thesaurus, Application Domain, Technology Topic, Popular Technical Reports.
© 2025 PatSnap. All rights reserved.Legal|Privacy policy|Modern Slavery Act Transparency Statement|Sitemap|About US| Contact US: help@patsnap.com