Method for manufacturing disc brake seat
A production method and technology for a brake disc seat, applied in the direction of brake parts, etc., can solve the problems of increased manufacturing cost, complicated mold design, long production cycle, etc., and achieve the effects of stable production process, overcoming waste of raw materials, and shortening production cycle.
- Summary
- Abstract
- Description
- Claims
- Application Information
AI Technical Summary
Problems solved by technology
Method used
Image
Examples
Embodiment Construction
[0022] The technical solutions of the present invention will be further specifically described below through the embodiments and in conjunction with the accompanying drawings.
[0023] figure 1 , figure 2 and image 3 Shown is an embodiment of a disc brake disc seat produced by the present invention. A disc brake disc seat is composed of a disc brake disc 1 and a fixing seat 2. The disc brake disc and the fixing seat are provided with screw holes and shaft holes. The shaft hole 3 on the fixing seat is a circular structure. The disc brake disc 1 can be screwed on the fixing seat 2, and a cavity 4 is arranged between the disc brake disc 1 and the fixing seat 2, and the shaft hole 6 of the disc brake disc 1 is connected to the liner 5, and the The disc brake disc and the liner are integral structures, and the shaft hole 6 of the disc brake disc 1 and the inner hole of the liner 5 are evenly distributed in the shaft hole by six sections of arc surfaces, forming six ballways. ...
PUM
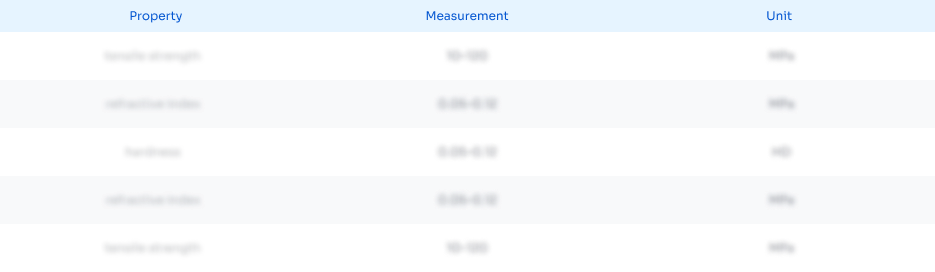
Abstract
Description
Claims
Application Information

- R&D Engineer
- R&D Manager
- IP Professional
- Industry Leading Data Capabilities
- Powerful AI technology
- Patent DNA Extraction
Browse by: Latest US Patents, China's latest patents, Technical Efficacy Thesaurus, Application Domain, Technology Topic, Popular Technical Reports.
© 2024 PatSnap. All rights reserved.Legal|Privacy policy|Modern Slavery Act Transparency Statement|Sitemap|About US| Contact US: help@patsnap.com