High-precision fast self-compensating method of automobile chassis dynamometer resistance simulation
A technology of automobile chassis and dynamometer, which is applied in the testing of vehicles, measuring devices, and testing of machine/structural components, etc., can solve the problems of low test efficiency and low resistance simulation accuracy.
Inactive Publication Date: 2009-11-25
CHINA TIANBO +1
View PDF0 Cites 4 Cited by
- Summary
- Abstract
- Description
- Claims
- Application Information
AI Technical Summary
Problems solved by technology
The purpose of the present invention is to solve the problems of low resistance simulation accuracy and low test efficiency caused by the nonlinear fluctuation of test data in the resistance simulation test of the automobile chassis dynamometer, and provide a high-precision resistance simulation of the automobile chassis dynamometer. fast self-compensation method
Method used
the structure of the environmentally friendly knitted fabric provided by the present invention; figure 2 Flow chart of the yarn wrapping machine for environmentally friendly knitted fabrics and storage devices; image 3 Is the parameter map of the yarn covering machine
View moreExamples
Experimental program
Comparison scheme
Effect test
Embodiment 1
the structure of the environmentally friendly knitted fabric provided by the present invention; figure 2 Flow chart of the yarn wrapping machine for environmentally friendly knitted fabrics and storage devices; image 3 Is the parameter map of the yarn covering machine
Login to View More PUM
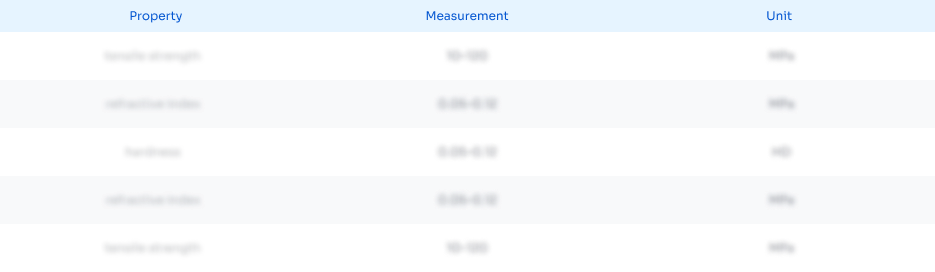
Abstract
The present invention provides a high-precision fast self-compensating method of automobile chassis dynamometer resistance simulation. According to the method, the test data is collected according to the index point and is standardized; then the characteristic space analysis is executed for calculating out the eigenvalue and the eigenvector; then the eigenvector corresponding with a maximum eigenvalue is calculated out; the eigenvector corresponding with the maximum eigenvalue is extracted; the contribution degree of the nonlinear input space, which is obtained by multiplying the eigenvector with a standard data sample, is marked as Gi, and the average value is represented as Gi, and the value of the contribution degree is obtained on this basis. Then the precision error e is calculated through the radio between a difference and the measured resistance, wherein the difference is between the measured resistance and the i-th simulated resistance. When the absolute value of e is larger than an anticipated control precision, taking e as a compensation precision modifying factor betai, and stopping the iteration otherwise. Finally the simulated resistance value on the chassis dynamometer is determined according to a formula and output for realizing the high-precision self-compensation of the chassis resistance. The method of the invention can greatly reduce the artificial subjective effect of the automobile chassis dynamometer in installation debugging and resistance simulation test, reduce the experiment number and increase the resistance simulation precision.
Description
【Technical field】: The invention relates to the technical field of automatic control, in particular to a bench high-precision resistance control technology for multi-working-condition emission tests of automobile chassis dynamometers. 【Background technique】: Automobile chassis dynamometer is an important device for overall testing of automobile dynamic characteristic parameters. It usually includes drum and mechanical system, data acquisition and conversion system, industrial computer real-time control system, database support system and human-computer interaction interface. The bench test process of the multi-condition emission test refers to the process of testing the vehicle's dynamic characteristics, fuel consumption and multi-condition emission indicators by simulating the road driving conditions on the indoor bench. In addition, the vehicle chassis dynamometer can also be used to easily adjust the load of the vehicle and diagnose the faults of the vehicle under load co...
Claims
the structure of the environmentally friendly knitted fabric provided by the present invention; figure 2 Flow chart of the yarn wrapping machine for environmentally friendly knitted fabrics and storage devices; image 3 Is the parameter map of the yarn covering machine
Login to View More Application Information
Patent Timeline

IPC IPC(8): G01M17/007
Inventor 王洪礼郭龙陶俊卫高强李志宏任立环
Owner CHINA TIANBO
Features
- Generate Ideas
- Intellectual Property
- Life Sciences
- Materials
- Tech Scout
Why Patsnap Eureka
- Unparalleled Data Quality
- Higher Quality Content
- 60% Fewer Hallucinations
Social media
Patsnap Eureka Blog
Learn More Browse by: Latest US Patents, China's latest patents, Technical Efficacy Thesaurus, Application Domain, Technology Topic, Popular Technical Reports.
© 2025 PatSnap. All rights reserved.Legal|Privacy policy|Modern Slavery Act Transparency Statement|Sitemap|About US| Contact US: help@patsnap.com